Podstawowa wiedza na temat oprzyrządowania do odlewania ciśnieniowego ze stopu aluminium
1. Podstawowa definicja oprzyrządowania do odlewania ciśnieniowego ze stopu aluminium
Produkcja form odnosi się do obróbki narzędzi do formowania i wykonywania półfabrykatów. Ponadto obejmuje również wykrojniki i oprzyrządowanie do wykrawania. Ogólnie oprzyrządowanie składa się z modułu górnego i modułu dolnego. Blacha stalowa jest umieszczana między górną a dolną matrycą, a materiał formowany jest pod wpływem prasy. Po otwarciu prasy uzyskany zostanie przedmiot obrabiany określony przez kształt oprzyrządowania lub odpowiedni odpad zostanie usunięty. Części tak małe jak złącza elektroniczne i tak duże jak deska rozdzielcza samochodu mogą być formowane za pomocą narzędzi.
Matryca progresywna to zestaw oprzyrządowania, który może automatycznie przenosić obrabiany przedmiot z jednej stacji na drugą i uzyskać część formującą na ostatniej stacji.
Proces oprzyrządowania obejmuje: wykrojnik, wykrojnik, wykrojnik złożony, wykrojnik, wykrojnik czterosuwowy, wykrojnik progresywny, wykrojnik, oprzyrządowanie do wykrawania itp.
2. Rodzaj oprzyrządowania
- (1) Oprzyrządowanie do tłoczenia metali: matryca ciągła, matryca pojedyncza, matryca złożona, matryca do rysowania
- (2) Forma do formowania tworzyw sztucznych: forma wtryskowa, forma do wytłaczania, forma ssąca
- (3) Oprzyrządowanie do odlewania ciśnieniowego: oprzyrządowanie do odlewania ciśnieniowego ze stopu cynku, oprzyrządowanie do odlewania ciśnieniowego ze stopu aluminium
- (4) Narzędzia do kucia
- (5) Oprzyrządowanie do metalurgii proszków
- (6) Oprzyrządowanie gumowe
3. Proces oprzyrządowania
- Cięcie: materiał przedniej matrycy, materiał tylnej matrycy, materiał wkładki, materiał na pozycję rzędu i materiał nachylonego przecisku;
- Otwarta rama: przednia rama formy i tylna rama formy;
- Otwarcie: otwarcie wnęki formy z przodu, otwarcie wnęki formy z tyłu, otwarcie linii podziału;
- Miedziany męski: przód miedziany męski, tylny miedziany męski, prześwit kątowy linii podziału miedziany męski;
- Cięcie drutu: wstaw linię podziału, miedziany męski, ukośna górna pozycja poduszki;
- Gongi komputerowe: linia podziału drobnych gongów, drobne gongi po rdzeniu;
- EDM: przednia forma gruba, miedziany męski, męskie czyszczenie kąta linii formy, tylna pozycja kości formy, pozycja poduszki;
- Wiercenie, otworek, naparstek; oprzyrządowanie górna pozycja linii do obróbki otworu otworowego, słup pozycji rzędu;
- Wierzchołek skośny, naparstek złożony, z naparstkami.
4 Inne
- (1) Chui, kod formy, gwóźdź na śmieci (gwóźdź graniczny);
- (2) Latający model;
- (3) Dysza, głowica podporowa, sprężyna i transport wody;
- (4) Pozycja zapisywania formy, polerowania, przedniej formy i tylnej formy kości;
- (5) Drobna struktura wody, hak śruby cięgła, sprężyna
- (6) Obróbka cieplna, hartowanie i azotowanie ważnych części;
5. Oprogramowanie narzędziowe
UGNX, Pro/NC, CATIA, master cam, SURFCAM, topsolid cam, space-e, camworks, worknc, tebis, hyperMILL, PowerMILL, gibbscam, featurecam itp.
6. Podstawowe funkcje
- (1) Para oprzyrządowania składa się na ogół z matrycy żeńskiej, stempla i podstawy matrycy, a niektóre z nich mogą być wieloczęściowymi modułami montażowymi. Dlatego połączenie górnych i dolnych matryc, połączenie wkładek i gniazd oraz montaż modułów wymaga dużej dokładności obróbki. Dokładność wymiarowa precyzyjnego oprzyrządowania często dochodzi do poziomu μm.
- (2) Powierzchnia kształtu niektórych produktów, takich jak części samochodowe, części do samolotów, zabawki i sprzęt gospodarstwa domowego, składa się z różnych zakrzywionych powierzchni, więc powierzchnia wnęki oprzyrządowania jest bardzo złożona. Niektóre powierzchnie wymagają obróbki matematycznej.
- (3) Produkcja małych oprzyrządowania w partii nie jest produkcją masową. W wielu przypadkach produkowana jest tylko jedna dostawa.
- (4) Istnieje wiele rodzajów procedur roboczych w procesie oprzyrządowania, takich jak frezowanie, wytaczanie, wiercenie, rozwiercanie i gwintowanie.
- (5) Stosowanie oprzyrządowania do powtarzalnej produkcji ma długą żywotność. Gdy para oprzyrządowania jest używana po przekroczeniu okresu eksploatacji, konieczna jest jego wymiana na nowe, więc produkcja oprzyrządowania jest często powtarzalna.
- (6) Czasami w produkcji profilowania nie ma rysunków ani danych, a przetwarzanie profilowania powinno odbywać się zgodnie z rzeczywistym przedmiotem. Wymaga to dużej precyzji i braku deformacji.
- (7) Materiały narzędziowe są doskonałe i mają wysoką twardość. Główne materiały narzędziowe wykonane są z wysokiej jakości stali stopowych, szczególnie tych o dużej trwałości, które często są wykonane ze stali ledeburytowej, takiej jak Crl2 i CrWMn. Ten rodzaj stali ma surowe wymagania od kucia półfabrykatu, obróbki do obróbki cieplnej. Dlatego nie można pominąć przygotowania technologii przetwarzania, deformacja obróbki cieplnej jest również poważnym problemem w przetwórstwie.
Zgodnie z powyższymi cechami dobór obrabiarek powinien w miarę możliwości odpowiadać wymaganiom obróbki. Na przykład funkcja systemu CNC powinna być silna, precyzja obrabiarki powinna być wysoka, sztywność powinna być dobra, stabilność termiczna powinna być dobra, a funkcja profilowania powinna być zapewniona.
7. Układ przepływu procesu
- (1) Przetwarzanie dolne, gwarancja ilości przetwarzania;
- (2) Wyrównanie wzorca odlewu pustego, kontrola naddatku powierzchni 2D, 3D;
- (3) Obróbka zgrubna profili 2D i 3D, nieinstalacyjna i nierobocza obróbka płaszczyzn (w tym powierzchnia platformy bezpieczeństwa, powierzchnia mocowania bufora, płaszczyzna płyty dociskowej i boczna płaszczyzna odniesienia);
- (4) Przed półwykańczaniem boczna płaszczyzna odniesienia powinna zostać prawidłowo znaleziona, aby zapewnić dokładność;
- (5) Obróbka półwykańczająca powierzchni 2D i 3D, obróbka wykańczająca wszelkiego rodzaju powierzchni roboczych instalacji (w tym powierzchnia montażowa bloku granicznego i powierzchnia styku, powierzchnia montażowa wkładki i tylna strona, powierzchnia montażowa stempla, powierzchnia montażowa frezu do odpadów i tylna strona, montaż sprężyny powierzchnia i powierzchnia styku, różne powierzchnie robocze ograniczające przesuw, powierzchnia montażowa klina i tylna powierzchnia), półwykończenie wszystkich rodzajów powierzchni prowadzących i otworów prowadzących oraz uwzględnienie wykańczania otworu odniesienia i wysokości odniesienia procesu oraz zapisywania danych;
- (6) Sprawdź i ponownie sprawdź dokładność obróbki;
- (7) Proces intarsji montera;
- (8) Przed zakończeniem wyrównaj płaszczyznę bazową otworu odniesienia procesu i sprawdź naddatek płytki;
- (9) Profil obróbki wykończeniowej 2D, 3D, profil stempla bocznego i pozycja otworu, otwór odniesienia procesu obróbki wykańczającej i punkt odniesienia wysokości, powierzchnia prowadząca obróbki wykończeniowej i otwór prowadzący;
- (10) Sprawdź i ponownie sprawdź dokładność obróbki.
8. Sprawy wymagające uwagi
(1) Przygotowanie procesu jest zwięzłe i szczegółowe, a treść przetwarzania jest wyrażona tak liczbowo, jak to możliwe;
(2) W przypadku kluczowych i trudnych punktów przetwarzania należy szczególnie podkreślić kunszt;
(3) Konieczne jest połączenie miejsc przetwarzania, a proces jest jasno wyrażony;
(4) Gdy wkładka musi być przetwarzana osobno, należy zwrócić uwagę na wymagania procesowe dotyczące dokładności przetwarzania;
(5) Po obróbce łączonej, dla części wkładek, które muszą być przetwarzane oddzielnie, proces jest wyposażony w wymagania wzorcowe dla oddzielnego przetwarzania podczas przetwarzania połączonego;
(6) Sprężyny najłatwiej ulegają uszkodzeniu podczas obróbki form, dlatego należy wybierać sprężyny do form o długiej trwałości zmęczeniowej.
Problemy z przetwarzaniem dużych form odlewniczych ze stopów aluminium
1. Ogromny rozmiar i waga
Podczas przetwarzania dużych form, jak radzić sobie z ich ogromnymi rozmiarami i wagą, jest głównym wyzwaniem stojącym przed firmami przetwórczymi. Przetwarzanie dużych form często wymaga dużego nakładu pracy, specjalnego sprzętu oraz wielu regulacji i mocowań, a na dokładność obróbki ma również wpływ wiele potencjalnych czynników, których nie można łatwo zagwarantować.
2. Kwestia kosztu nabycia
Największym kosztem bezpośrednio związanym z obróbką i produkcją różnych dużych form jest koszt zakupu obrabiarki. Obrabiarka, która może wytwarzać duże formy, jest dość droga, zwłaszcza w przypadku złożonego układu procesowego, do wykonania wszystkich procesów od obróbki zgrubnej do wykańczania formy potrzebnych jest wiele obrabiarek. Tak wysokie wczesne koszty nakładów są również największą przeszkodą dla wielu firm w wejściu na ten rynek. Z tego widać, że jeśli obróbka zgrubna i wykańczająca dużych form może być zrealizowana na odpowiedniej obrabiarce, nawet jeśli wymagane jest tylko jedno debugowanie i mocowanie, wówczas wiele problemów zostanie rozwiązanych i można zagwarantować dokładność obróbki.
Centrum obróbkowe
1. Konstrukcja łoża żeliwnego, wrzeciono obrabiarki ma funkcję rozpraszania ciepła;
Materiał żeliwny ma wysoką sztywność i właściwości rozpraszania ciepła, dzięki czemu jest najbardziej stabilnym materiałem do wytwarzania konstrukcji obrabiarek. Każda obrabiarka używana do frezowania dużych części musi mieć w pierwszej kolejności bardzo mocną konstrukcję żeliwną i być wyposażona we wrzeciono z funkcją rozpraszania ciepła.
Jeśli chodzi o wał główny obrabiarki, musi on wykorzystywać wbudowaną technologię chłodzenia, aby chłodzić wał główny z zewnątrz łożyska, aby sam wał główny nie uległ spaleniu lub utracił precyzję z powodu temperatury ekspansja podczas długotrwałej obróbki. Czynniki te są bardzo ważne, ponieważ obróbka dużych form zajmuje dużo czasu, a przy ciężkich warunkach skrawania zwiększy to ciepło i naprężenia formy. Dlatego elementy konstrukcyjne obrabiarki muszą mieć dobrą sztywność i charakterystykę rozpraszania ciepła, co jest warunkiem wstępnym do obróbki wysokiej jakości form odlewniczych ze stopów aluminium na dużą skalę. Dlatego konieczne jest jak największe ograniczenie drgań obrabiarki podczas procesu obróbki oraz szybkie odprowadzenie ciepła wytworzonego podczas procesu obróbki. Wybór odpowiednich obrabiarek i narzędzi do obróbki może zapewnić korzystną sytuację pod względem kosztów i czasu cyklu.
2. Technologia stabilności termicznej
Ze względu na długi czas obróbki należy również uwzględnić wpływ temperatury otoczenia. Na przykład, obróbka dużej formy odlewniczej ze stopu aluminium na zwykłej obrabiarce, gdy temperatura otoczenia zmienia się o 10°C, spowoduje zmianę temperatury o 6°C w kolumnie obrabiarki, co spowoduje zmianę o 0.07 mm równoległość płyty kątowej wrzeciona. Dlatego projekt obrabiarki musi uwzględniać wpływ temperatury otoczenia, aby uniknąć wpływu temperatury otoczenia na dokładność obrabianych części.
3. Prędkość
W przypadku dużego centrum obróbczego form, które może się szybko poruszać, prędkość wrzeciona obrabiarki do dużych form powinna osiągnąć co najmniej 20000 obr / min, a prędkość cięcia metalu powinna wynosić 762 ~ 20000 mm / min.
4. Precyzja
Precyzyjna kontrola zawsze przebiega przez wszystkie etapy obróbki formy. Jeśli potrzebujesz wykonać obróbkę zgrubną i wykańczającą dużych form na centrum obróbczym, musisz ściśle kontrolować dokładność pozycjonowania i powtarzać dokładność pozycjonowania obrabiarki. Centrum obróbcze dedykowane do dużych form ma generalnie dokładność pozycjonowania ±1.5μm, a powtarzalną dokładność pozycjonowania ±1μm. Jednocześnie jego dokładność skoku powinna być utrzymywana w granicach 5 μm.
5. Rozdzielczość opinii
W przypadku precyzyjnej obróbki powierzchni rozdzielczość sprzężenia zwrotnego samej obrabiarki jest bardzo ważna dla wykrywania dokładności obrabianych części. Przy standardowej rozdzielczości sprzężenia zwrotnego 1μm zwykle uzyskiwane wyniki nie są zbyt satysfakcjonujące. Jeśli rozdzielczość może osiągnąć 0.05 μm, to efekt końcowy jest prawie bez wad. Co więcej, poprzez kontrolę rozdzielczości obrabiarki, sprzężenia zwrotnego skali i śrub kulowych o małym skoku można jeszcze bardziej poprawić jakość obróbki powierzchni części.
6. Wrzeciono
Wrzeciono zastosowane na wielkoformatowym centrum obróbczym form musi spełniać wymagania obróbki zgrubnej, półwykańczającej i wysokiej jakości wykańczającej, a jako wzorzec odniesienia jakość obróbki powierzchni jaką można osiągnąć powinna być kontrolowana na poziomie 2μm. Zwykle jest to bardzo ważne dla wykończenia powierzchni zamykającej formy i części linii podziału, ale w tradycyjnej technologii wielu producentów form musi stosować ręczne polerowanie, aby nadrobić brak dokładności obróbki narzędzia. Ponieważ produkcja obrabiarek do obróbki na dużą skalę jest kosztowna, zakup wielofunkcyjnej obrabiarki do tego procesu jest oczywiście niepraktyczny.
Ponadto rozsądna konstrukcja wrzeciona musi być w stanie zmaksymalizować żywotność narzędzia, aby mogło ono kontynuować pracę przy niskich wibracjach i niewielkim wzroście temperatury podczas cyklu obróbki. Na przykład podczas obróbki form deski rozdzielczej samochodów na dużym centrum obróbczym form, jeśli do narzędzi wykańczających używana jest płytka 16 mm CBN, prędkość obróbki może osiągnąć 8 m/min, żywotność przekracza 30 godzin, a jakość obrabianej powierzchni może być kontrolowana w granicach 0.336 ~ 3.2 μm. Widać, że biorąc pod uwagę wzrost kosztów narzędzi przy obróbce dużych form, zastosowanie specjalnie zaprojektowanych obrabiarek do obróbki dużych form może nie tylko przedłużyć żywotność narzędzi, ale także zaoszczędzić wiele kosztów narzędzi przy obróbce każdej formy .
7. Ruchoma wieloosiowa głowica obróbkowa
Ze względu na ograniczenia wielkości i wagi formy, zwykle mocowanie przedmiotu obrabianego zajmuje dużo czasu. Dlatego zastosowanie 3-osiowego centrum obróbczego nie tylko zmniejsza ilość odpluskwiania i czasów mocowania przedmiotu obrabianego, ale również nie wpływa na dokładność obróbki obrabiarki, tym samym znacznie poprawiając zdolność produkcyjną warsztatu do obróbki dużych formy.
Ruchoma wieloosiowa głowica obróbkowa może być używana do obróbki dużych form o szczególnie złożonych strukturach. Głowica obróbkowa zaprojektowana zgodnie ze zmienną geometrią umożliwia 3-osiową obróbkę symultaniczną. Do frezowania i obróbki głębokich wgłębień można użyć tylko jednego mocowania przedmiotu obrabianego. Formy i otwory chłodzące, a także wycinanie wielu innych części o skomplikowanej geometrii. Na przykład, gdy wrzeciono jest nachylone pod optymalnym kątem, można zwiększyć bliskość głowicy obróbkowej do punktu obróbki frezarskiej, dzięki czemu wieloosiową głowicę obróbkową można wykorzystać do zakończenia obróbki ukośnego otworu.
Ponadto, ponieważ wieloosiowa głowica obróbkowa obrabia powierzchnię przedmiotu obrabianego, zamiast ostrza zastosowano krawędź promieniową narzędzia, dzięki czemu można poprawić chropowatość powierzchni.
8. Zarządzanie wiórami
Podczas cięcia metalu będzie generowana duża ilość wiórów. Jeśli nie da się go wyeliminować na czas, nieuchronnie doprowadzi to do wtórnego skrawania i spowoduje wzrost temperatury części konstrukcyjnych obrabiarki lub powierzchni przedmiotu obrabianego. Pod stołem roboczym dużego centrum obróbczego form znajduje się zwykle 18 otworów na wióry, niezależnie od tego, gdzie stół jest przesuwany, wióry można niezawodnie usuwać. W obrabiarce znajdują się 4 wbudowane zawiasowe przenośniki wiórów, które z dużą prędkością wysyłają wióry do przodu obrabiarki.
9. Chłodziwo pod wysokim ciśnieniem
Podczas obróbki dużych form bardzo ważną rolę odgrywa chłodziwo pod wysokim ciśnieniem. Na przykład, przy użyciu metody obróbki 2+3 osi do wiercenia otworów skośnych, do skutecznego usuwania wiórów i uzyskania wyższej precyzji skrawania wymagane jest chłodziwo o ciśnieniu 1000 psi (1 psi=6890 Pa). Jeśli nie ma takiego chłodziwa pod wysokim ciśnieniem, podczas obróbki nachylonych otworów należy dodać dodatkowe obrabiarki, wymagana jest instalacja wtórna, co zmniejsza dokładność obróbki i zwiększa koszty cyklu. Zgodnie z powyższą analizą widać, że prosta obróbka dużych form wymaga, aby obrabiarka miała coraz więcej i lepsze funkcje. Nowe 2516-osiowe poziome centrum obróbkowe MCC3VG opracowane przez Makino, prędkość wrzeciona może osiągnąć 15000 obr/min i przyjmuje metodę „chłodzenia rdzenia wału” i funkcję „smarowania ciśnieniowego łożyska”, aby zapewnić, że wrzeciono i dołączone łożyska mogą schłodzić się na czas i skutecznie.
Ponadto wał główny może poruszać się nie tylko wzdłuż poziomej osi X, pionowej osi Y oraz kierunku przedniej i tylnej osi Z, ale może również obracać się wraz z osią A i osią C. Dzięki dwóm funkcjom indeksowania może nie tylko zmniejszyć nakład pracy przy regulacji, ale także ciąć skomplikowane elementy, takie jak zderzaki, tablice przyrządów i soczewki reflektorów samochodowych.
Proszę zachować źródło i adres tego artykułu do przedruku:Podstawowa wiedza na temat oprzyrządowania do odlewania ciśnieniowego ze stopu aluminium
Minhe Firma odlewnicza są dedykowane do produkcji i zapewniania wysokiej jakości i wysokiej wydajności części odlewniczych (zakres części odlewanych z metalu obejmuje głównie) Cienkościenne odlewanie ciśnieniowe,Odlewanie pod ciśnieniem z komory gorącej,Odlewanie matrycowe w zimnej komorze), Usługa okrągła (usługa odlewania ciśnieniowego,Obróbka CNC,Produkcja form, Obróbka powierzchni). Wszelkie niestandardowe odlewanie ciśnieniowe z aluminium, odlewanie ciśnieniowe magnezu lub znalu / cynku oraz inne wymagania dotyczące odlewów są mile widziane, aby się z nami skontaktować.
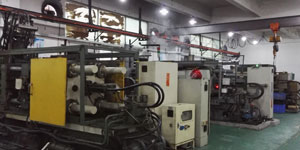
Pod kontrolą ISO9001 i TS 16949, wszystkie procesy są przeprowadzane przez setki zaawansowanych maszyn do odlewania ciśnieniowego, maszyn 5-osiowych i innych urządzeń, od blasterów po pralki Ultra Sonic. Minghe ma nie tylko zaawansowany sprzęt, ale także profesjonalny zespół doświadczonych inżynierów, operatorów i inspektorów, aby zrealizować projekt klienta.
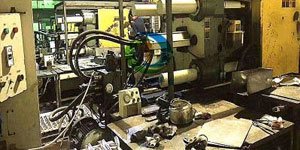
Producent kontraktowy odlewów ciśnieniowych. Możliwości obejmują odlewanie ciśnieniowe aluminium w zimnej komorze od 0.15 funta. do 6 funtów, szybka zmiana konfiguracji i obróbka. Usługi o wartości dodanej obejmują polerowanie, wibrowanie, gratowanie, śrutowanie, malowanie, powlekanie, powlekanie, montaż i oprzyrządowanie. Obrabiane materiały obejmują stopy takie jak 360, 380, 383 i 413.
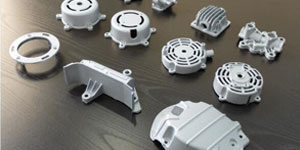
Pomoc w projektowaniu odlewów cynkowych/równoległe usługi inżynieryjne. Zleceniodawca precyzyjnych odlewów cynkowych. Można wytwarzać miniaturowe odlewy, odlewy ciśnieniowe wysokociśnieniowe, odlewy wielopłytkowe, konwencjonalne odlewy formowe, odlewy jednostkowe i niezależne oraz odlewy z uszczelnieniem gniazdowym. Odlewy mogą być produkowane w długościach i szerokościach do 24 cali z tolerancją +/- 0.0005 cala.
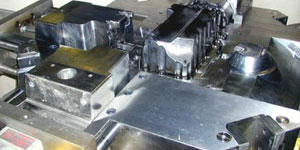
Certyfikowany ISO 9001: 2015 producent odlewanego magnezu, Możliwości obejmują odlewanie ciśnieniowe magnezu do 200 ton gorącej komory i 3000 ton zimnej komory, projektowanie oprzyrządowania, polerowanie, formowanie, obróbka skrawaniem, malowanie proszkowe i płynne, pełna kontrola jakości z możliwościami CMM , montaż, pakowanie i dostawa.
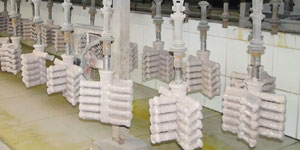
Certyfikat ITAF16949. Dodatkowa usługa odlewania obejmuje casting inwestycyjny,odlewanie piaskowe,Odlewanie grawitacyjne, Utracone odlewanie pianki,Odlewanie odśrodkowe,Odlewanie próżniowe,Trwałe odlewanie form,.Możliwości obejmują EDI, pomoc inżynierską, modelowanie bryłowe i przetwarzanie wtórne.
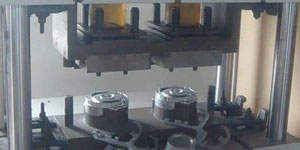
Przemysł odlewniczy Części Studia przypadków dla: samochodów, rowerów, samolotów, instrumentów muzycznych, jednostek pływających, urządzeń optycznych, czujników, modeli, urządzeń elektronicznych, obudów, zegarów, maszyn, silników, mebli, biżuterii, przyrządów, telekomunikacji, oświetlenia, urządzeń medycznych, urządzeń fotograficznych, Roboty, rzeźby, sprzęt dźwiękowy, sprzęt sportowy, narzędzia, zabawki i inne.
W czym możemy Ci pomóc dalej?
∇ Przejdź do strony głównej dla Odlewanie ciśnieniowe Chiny
→Części odlewnicze-Dowiedz się, co zrobiliśmy.
→Powiązane wskazówki dotyczące Usługi odlewania ciśnieniowego
By Producent odlewów ciśnieniowych Minghe |Kategorie: Przydatne artykuły |Materiał tagi: Odlewanie aluminium, Odlew cynkowy, Odlewanie magnezu, Casting tytanu, Odlewanie ze stali nierdzewnej, Odlew mosiężny,Odlew z brązu,Przesyłanie wideo,Historia firmy,Odlew aluminiowy |Komentarze wyłączone