Różne czynniki wpływające na stabilność wymiarową odlewów inwestycyjnych
Ciągłe podnoszenie dokładności wymiarowej odlewów metodą traconego wosku oraz zmniejszanie ilości odpadów powstałych w wyniku przewymiarowania było od zawsze jednym z głównych celów realizowanych przez odlewników metodą traconego wosku w kraju i za granicą.
1. Stabilność wymiarowa odlewów inwestycyjnych
1. Stabilność wymiarowa modelu woskowego i czynniki na niego wpływające
W większości przypadków rozmiar formy woskowej zmienia się znacznie, gdy zmienia się rozmiar odlewu, i jest kilka wyjątków. Ogólnie rzecz biorąc, fluktuacja wielkości formy woskowej odpowiada za 10% do 70% fluktuacji wielkości odlewu.
Parametry procesu formowania mają decydujący wpływ na stabilność wymiarową formy woskowej. Główne czynniki to:
(1) Temperatura prasowania wosku
Różne materiały do formowania mają różne właściwości ze względu na wpływ temperatury prasowania wosku. W przypadku stosowania materiałów formierskich na bazie wosku temperatura prasowania wosku jest bardzo wrażliwa na wpływ stabilności wymiarowej formy woskowej, podczas gdy materiały formierskie na bazie żywic mają mniejszy wpływ.
(2) Ciśnienie wtrysku
Gdy ciśnienie jest małe, szybkość skurczu formy woskowej znacznie spada wraz ze wzrostem ciśnienia. Jednak po pewnym zwiększeniu ciśnienia (≥1.6 MPa) ciśnienie prawie nie ma wpływu na wielkość formy woskowej. Nic dziwnego, że zagraniczne wyniki badań często stwierdzają, że „ciśnienie nie ma nic wspólnego z wielkością formy woskowej”, ale wrażenie wielu krajowych firm nie jest takie samo.
(3) Natężenie przepływu
Natężenie przepływu materiału formy można zmienić na dwa sposoby, ale wpływ na wielkość formy woskowej nie jest taki sam:
·Zmieniając ustawienie prędkości przepływu prasy woskowej, metoda ta ma niewielki wpływ na kurczenie się formy woskowej. Ma jednak istotny wpływ na wypełnienie i jakość powierzchni elementów cienkościennych o skomplikowanych kształtach lub form woskowych z rdzeniami.
·Ta metoda ma duży wpływ na zmianę pola przekroju portu wtrysku wosku, ponieważ zwiększenie pola przekroju portu wtrysku wosku może nie tylko obniżyć temperaturę prasowania wosku, ale również przedłużyć krzepnięcie czas materiału formy w porcie wtryskowym wosku, zwiększając tym samym zagęszczenie formy woskowej. Zmniejsza się stopień skurczu i skurcz powierzchniowy.
(4) Czas wtrysku
Tak zwany czas wtrysku obejmuje tutaj trzy okresy napełniania, zagęszczania i konserwacji. Czas napełniania odnosi się do czasu, w którym materiał do formowania wypełnia wnękę formującą; zagęszczenie odnosi się do czasu od napełnienia wypraski do zamknięcia dyszy wtryskowej wosku; a trzymanie odnosi się do czasu od zamknięcia dyszy wtryskowej wosku do wyrzucenia formy.
Czas wtrysku ma istotny wpływ na szybkość skurczu formy woskowej. Dzieje się tak dlatego, że więcej materiału formy może zostać wciśnięte do gniazda poprzez wydłużenie czasu wtrysku, a forma woskowa będzie bardziej zagęszczona, zmniejszając w ten sposób szybkość skurczu. Waga modelu woskowego wzrasta wraz z wydłużonym czasem zagęszczania. Czas zagęszczania powinien być odpowiedni. Jeśli czas zagęszczania jest zbyt długi, materiał formy w porcie do wtrysku wosku całkowicie się zestalił i zagęszczanie nie będzie działać. Na rysunku 4 widać również, że gdy czas wtrysku jest krótki (15-25 s), temperatura prasowania wosku wzrasta, a szybkość skurczu wzrasta; ale przy wydłużeniu czasu wtrysku do 25-35s (przy założeniu, że czas napełniania pozostaje stały, rzeczywisty Powyżej ma na celu wydłużenie czasu zagęszczania) Wpływ temperatury prasowania wosku staje się mniejszy; gdy czas wtrysku wzrośnie do ponad 35 s, wystąpi sytuacja odwrotna, to znaczy, gdy temperatura prasowania wosku wzrośnie, zamiast tego zmniejszy się szybkość skurczu formy woskowej. Zjawisko to można wytłumaczyć tym, że zwiększenie temperatury materiału formy i wydłużenie czasu zagęszczania daje taki sam efekt jak zwiększenie stopnia zagęszczenia formy woskowej.
(5) Temperatura formowania i sprzęt do prasowania wosku
Temperatura formowania jest wysoka, forma woskowa powoli stygnie, a stopień skurczu wzrasta. Dzieje się tak, ponieważ forma woskowa nadal znajduje się w formowaniu tłocznym przed wyrzuceniem formy, a skurcz jest ograniczony, ale po wyrzuceniu formy może się swobodnie kurczyć. Dlatego też, jeśli temperatura formy woskowej jest wysoka, gdy forma jest zwalniana, końcowy stopień skurczu będzie duży i odwrotnie, stopień skurczu będzie mały.
W ten sam sposób układ chłodzenia prasy woskowej może mieć wpływ około 0.3% na wielkość formy woskowej.
Na koniec warto podkreślić, że przy stosowaniu materiałów do form na bazie wosku, pasta woskowa jest trójfazowym układem współistnienia ciała stałego, cieczy i gazu. Stosunek objętości między trzema fazami ma duży wpływ na wielkość formy woskowej. Zależności proporcjonalnej między tymi trzema nie można kontrolować w rzeczywistej produkcji, co jest również ważnym powodem słabej stabilności wymiarowej form woskowych przy użyciu materiałów formierskich opartych na wosku.
2. Wpływ materiału skorupy i procesu wytwarzania skorupy na stabilność wymiarową odlewów
Wpływ płaszcza formy na wielkość odlewu spowodowany jest głównie rozszerzalnością cieplną i odkształceniem termicznym (pełzanie pod wpływem wysokiej temperatury) płaszcza formy podczas wypalania oraz ograniczeniem (zatkaniem) płaszcza formy na skurcz chłodzący odlew.
(1) Rozszerzalność cieplna powłoki
Głównie zależy od materiału powłoki. Różne materiały ogniotrwałe mają różne szybkości rozszerzania. Wśród powszechnie stosowanych materiałów ogniotrwałych najniższa szybkość ekspansji ma topiona krzemionka, następnie krzemian glinu, a krzemionka jest największa i nierówna. Po przetestowaniu ustalono, że powłoka z krzemianu glinu może być podgrzewana od temperatury pokojowej do 1000 ℃, powłoka może wytworzyć około 0.25% ekspansji, co stanowi niewielką część całkowitego skurczu rozmiaru odlewu. Dlatego też, jeśli stosuje się takie materiały ogniotrwałe, powłoka ma lepszą stabilność wymiarową, taka jak topiona krzemionka będzie niewątpliwie lepsza. Jednakże, jeśli stosuje się krzemionkę, wielkość skorupy znacznie się zmienia.
(2) Odkształcenie termiczne (pełzanie w wysokiej temperaturze)
Na przykład powłoka wykorzystująca szkło wodne jako spoiwo ma znacznie wyższy stopień pełzania w wysokich temperaturach powyżej 1000°C niż powłoki z zolu krzemionkowego i krzemianu etylu. Chociaż sam stopiony korund ma wysoką ogniotrwałość, ze względu na obecność zanieczyszczeń, takich jak tlenek sodu, temperatura wypalania powłoki wyższa niż 1000 ℃ może również powodować pełzanie, co powoduje słabą stabilność wymiarową.
(3) Ograniczenie skorupy formy do skurczu odlewu – cofanie się i zapadanie skorupy formy Zależy to również głównie od materiału skorupy formy.
Podsumowując, materiały ogniotrwałe odgrywają główną rolę we wpływie skorupy na zmiany wielkości odlewu, ale nie można ignorować roli spoiwa. Natomiast wpływ procesu wytwarzania muszli jest niewielki.
3. Wpływ naprężeń wywołanych nierównomiernym chłodzeniem odlewów na stabilność wymiarową
Szybkość chłodzenia każdej części odlewu (w tym systemu bramkowania) jest inna, co generuje naprężenia termiczne i deformuje odlew, wpływając tym samym na stabilność wymiarową. Jest to często spotykane w rzeczywistej produkcji. Zmniejszenie szybkości stygnięcia odlewów i ulepszenie kombinacji bieżników to skuteczne środki zapobiegawcze.
2. Klucz do poprawy dokładności - szybkość skurczu formy jest przypisany poprawnie
Wspomniana powyżej „stabilność wymiarowa” różni się od „dokładności wymiarowej” i „precyzji (precyzji)”. Stabilność wymiarowa (tj. precyzja) jest równoznaczna ze spójnością wymiarową, odzwierciedlającą stopień fluktuacji wymiarowej lub dyspersji i jest zwykle mierzona przez odchylenie standardowe σ. Główną przyczyną niestabilności wymiarowej jest luźna kontrola procesu, która jest błędem losowym. Dokładność odnosi się do stopnia, w jakim średnia arytmetyczna wielu zmierzonych wartości odbiega od wielkości nominalnej dla określonego rozmiaru odlewu, czyli wielkości odchylenia średniego. W przypadku odlewania metodą traconego wosku główną przyczyną słabej dokładności wymiarowej jest niewłaściwe przypisanie stopnia skurczu podczas projektowania profilowania, co jest błędem systematycznym, który zwykle jest korygowany poprzez wielokrotne naprawy formy. Dokładność wymiarowa (precyzja) jest kombinacją dwóch powyższych. Dlatego, aby poprawić dokładność wymiarową odlewów i rozwiązać problem tolerancji wielkości produktu, nie tylko proces musi być ściśle kontrolowany w celu zmniejszenia wahań wymiarowych, ale także szybkość skurczu każdego wymiaru odlewu musi być prawidłowo przypisana podczas projektowania profilu .
Powszechnie wiadomo, że ostateczny skurcz całkowity odlewów precyzyjnych jest kombinacją formy woskowej, skurczu stopu i niewielkiej ekspansji skorupy. Powłoka pęcznieje o około 0.25%, a jej działanie jest ograniczone. Chociaż liniowy wskaźnik skurczu stopu jest często większy niż skurczu formy woskowej, to fluktuacja wymiarów spowodowana procesem prasowania wosku ma większy wpływ. W celu obniżenia kosztów naprawy formy i zmniejszenia wahań wielkości odlewu bardzo ważne jest kontrolowanie szybkości skurczu formy woskowej.
1. Skurcz formy woskowej
Skurcz formy woskowej należy mierzyć po całkowitym ustabilizowaniu wielkości formy woskowej. Dzieje się tak, ponieważ kurczenie się formy woskowej nie zatrzymuje się całkowicie po wyrzuceniu formy. Rozmiar formy woskowej czasami stabilizuje się dopiero po kilku dniach od wyrzucenia formy. Jednak większość skurczu materiału formy jest zasadniczo zakończona w ciągu jednej do kilku godzin po wyrzuceniu formy. Na szybkość skurczu formy woskowej wpływają głównie następujące czynniki:
(1) Rodzaj materiału formy;
(2) Przekrój modelu woskowego;
Warto podkreślić, że wielkość przekroju formy woskowej ma istotny wpływ na szybkość skurczu. Na przykład szybkość skurczu typowego niewypełnionego materiału formy podczas prasowania form woskowych o różnych grubościach. Grubość sekcji formy woskowej generalnie nie powinna przekraczać 13 mm. Gdy grubość jest większa niż 13 mm, grubość ścianki można zmniejszyć, stosując bloki wosku na zimno lub rdzenie metalowe, aby osiągnąć cel zmniejszenia skurczu, co jest szczególnie ważne w przypadku materiałów do form bez wypełniaczy.
Uwaga: 1. Szybkość skurczu rozpuszczalnego w wodzie materiału formy wynosi około 0.25%;
2. W przypadku stosowania rdzeni rozpuszczalnych, rdzeni ceramicznych lub rurek ze szkła kwarcowego nie występuje liniowy skurcz formy woskowej stykającej się z rdzeniem;
(3) Rodzaje rdzeni
Wielkość gniazda formy woskowej jest niewątpliwie zgodna z kształtem rdzenia. Dlatego zastosowanie rdzeni stało się sposobem na poprawę dokładności wymiarowej wnęki formy woskowej.
2. Skurcz stopu
Skurcz stopu zależy głównie od następujących czynników:
· Rodzaj stopu odlewniczego i skład chemiczny;
· Geometria odlewu (w tym stan ograniczenia i rozmiar przekroju);
· Parametry odlewania, takie jak temperatura odlewania, temperatura skorupy, szybkość chłodzenia odlewu itp.;
· Zastosowanie rdzeni ceramicznych, rurek ze szkła kwarcowego itp.
Ponieważ temperatura odlewania, temperatura skorupy, szybkość chłodzenia odlewu i inne parametry procesu są na ogół ściśle kontrolowane przez standardowe karty procesowe podczas procesu produkcyjnego, spowodowane tym wahania wielkości nie są duże między różnymi partiami produkcyjnymi. Nawet jeśli temperatura odlewania przekracza zakres wymagany przez specyfikację procesu, wahania wielkości odlewu zwykle nie są duże. Podobnie jak w przypadku formy woskowej, wielkość przekroju odlewu i ograniczenia powłoki formy są głównymi czynnikami wpływającymi na skurcz stopu. Doświadczenie pokazuje, że stopień skurczu całkowicie ograniczonego rozmiaru wynosi od 85% do 89% stopnia swobodnego skurczu; rozmiar częściowo ograniczony wynosi od 94% do 95%.
3. Minimalna liczba pierwszej partii próbek do pomiaru
Wymieniony powyżej współczynnik skurczu jest danymi empirycznymi opartymi na wcześniejszych doświadczeniach, a nie rzeczywistym współczynnikiem skurczu. Zaprojektuj i wyprodukuj formy zgodnie z tymi danymi, naprawa jest nieunikniona. Aby poprawić dokładność i skuteczność napraw oraz zmniejszyć liczbę napraw, kluczowym ogniwem jest dokładne sprawdzenie wielkości wystarczającej liczby próbnych próbek odlewniczych. Ponieważ wielkość produkowanych przez nas odlewów nie może być dokładnie taka sama, więc tylko przy odpowiednio dużej ilości zmierzonych próbek uzyskana wartość średnia może być zbliżona do prawdziwej średniej arytmetycznej. Na tej podstawie nietrudno zauważyć, że minimalna liczba próbek pomiarowych jest bezpośrednio związana ze zdolnością procesu produkcyjnego do kontrolowania spójności wielkości produktu (zdolność procesu). Jeżeli odlewy są całkowicie tej samej wielkości, wystarczy zbadać tylko jedną próbkę; I odwrotnie, jeśli wielkość odlewu znacznie się zmienia,
Aby uzyskać dokładniejsze dane dotyczące skurczu, konieczne jest zmierzenie wielu próbek. Jak wspomniano wcześniej, zdolność procesu produkcyjnego do kontrolowania rozmiaru może być reprezentowana przez 6σ rozmiaru odlewu wytworzonego w tym procesie. Z obecnego poziomu technologicznego większości odlewni inwestycyjnych, Hp jest przeważnie powyżej 0.5, więc pierwsza partia próbek pomiarowych wymaga generalnie co najmniej 11 próbek.
trzy. Analiza systemu pomiarowego
Analizując i rozwiązując problemy z wielkością produktu, musimy zwrócić uwagę na dokładność i wiarygodność zastosowanego systemu pomiarowego. Poza częstą kalibracją samych przyrządów i urządzeń pomiarowych ważne jest również minimalizowanie błędów pomiarowych. Jeśli system pomiarowy (łącznie z operatorem i metodą obsługi) ma duży błąd, nie tylko odrzuty mogą być ocenione jako kwalifikowane produkty, ale także wiele kwalifikowanych produktów może być błędnie ocenionych jako odrzuty, co może spowodować poważne awarie lub niepotrzebne ekonomiczne straty. Najprostszym sposobem określenia, czy system pomiarowy nadaje się do określonego zadania pomiarowego, jest wykonanie testów kwalifikacyjnych odtwarzalności i powtarzalności. Tak zwana powtarzalność oznacza, że ten sam inspektor używa tego samego przyrządu (lub sprzętu) i metody do sprawdzenia tej samej części i uzyskania spójności wyników. Odtwarzalność odnosi się do spójności wyników uzyskanych przez różnych operatorów przy użyciu różnych przyrządów do sprawdzania tej samej części. American Automotive Industry Action Group (Automotive Industry Action Group) określa, że procent zintegrowanego odchylenia standardowego powtarzalności i odtwarzalności R&R w odchyleniu standardowym mierzonych fluktuacji wielkości odlewu wynosi ≤30% jako standard dla systemu pomiarowego, aby spełnić wymagania [5]. W pomiarach niektórych odlewów o dużych rozmiarach i skomplikowanych kształtach nie wszystkie systemy pomiarowe mogą spełnić to wymaganie. Dopuszczalny błąd pomiaru przy pomiarze form powinien być mniejszy, zwykle 1/3.
cztery. Struktura formy i poziom przetwarzania
Powszechnie wiadomo, że struktura formy i jakość obróbki mają istotny wpływ na wielkość i geometrię formy woskowej. Na przykład, czy mechanizm pozycjonowania i zaciskania jest dokładny i niezawodny, czy pasujący luz ruchomych części (takich jak ruchome bloki, śruby itp.) jest odpowiedni, czy metoda ciągnienia jest korzystna dla zapewnienia dokładności wymiarowej odlewów itd. Nie trzeba dodawać, że w przypadku znacznej liczby krajowych zakładów odlewania metodą traconego wosku poziom projektowania i produkcji form nadal wymaga pilnej poprawy.
Piątki. na zakończenie
Z powyższej analizy nietrudno zauważyć, że poprawa dokładności wymiarowej odlewów metodą traconego wosku jest systematycznym przedsięwzięciem obejmującym wszystkie aspekty procesu produkcji odlewów metodą traconego wosku. Główne punkty można podsumować w następujący sposób:
1) Ściśle kontrolować parametry procesu formowania, zwłaszcza te, które mają istotny wpływ na wielkość odlewu.
2) Wybierz odpowiedni materiał powłoki.
3) Zbierz, policz i przeanalizuj dane związane ze skurczem we właściwej metodzie, zgodnej z zasadami statystycznymi, aby poprawić dokładność przypisania skurczu.
4) Często monitoruj system pomiarowy (w tym sprzęt, personel kontrolny i technologię), aby zapewnić, że błędy powtarzalności i odtwarzalności spełniają określone wymagania.
5) Ciągle ulepszaj poziom projektowania i produkcji form.
6) Środki takie jak korekta odlewu i stabilizacja obróbki cieplnej są nadal niezbędne w wielu przypadkach
Proszę zachować źródło i adres tego artykułu do przedruku: Różne czynniki wpływające na stabilność wymiarową odlewów inwestycyjnych
Minhe Firma odlewnicza są dedykowane do produkcji i zapewniania wysokiej jakości i wysokiej wydajności części odlewniczych (zakres części odlewanych z metalu obejmuje głównie) Cienkościenne odlewanie ciśnieniowe,Odlewanie pod ciśnieniem z komory gorącej,Odlewanie matrycowe w zimnej komorze), Usługa okrągła (usługa odlewania ciśnieniowego,Obróbka CNC,Produkcja form, Obróbka powierzchni). Wszelkie niestandardowe odlewanie ciśnieniowe z aluminium, odlewanie ciśnieniowe magnezu lub znalu / cynku oraz inne wymagania dotyczące odlewów są mile widziane, aby się z nami skontaktować.
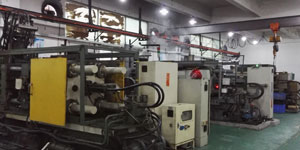
Pod kontrolą ISO9001 i TS 16949, wszystkie procesy są przeprowadzane przez setki zaawansowanych maszyn do odlewania ciśnieniowego, maszyn 5-osiowych i innych urządzeń, od blasterów po pralki Ultra Sonic. Minghe ma nie tylko zaawansowany sprzęt, ale także profesjonalny zespół doświadczonych inżynierów, operatorów i inspektorów, aby zrealizować projekt klienta.
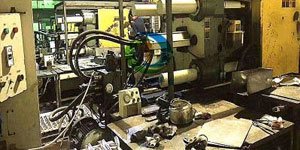
Producent kontraktowy odlewów ciśnieniowych. Możliwości obejmują odlewanie ciśnieniowe aluminium w zimnej komorze od 0.15 funta. do 6 funtów, szybka zmiana konfiguracji i obróbka. Usługi o wartości dodanej obejmują polerowanie, wibrowanie, gratowanie, śrutowanie, malowanie, powlekanie, powlekanie, montaż i oprzyrządowanie. Obrabiane materiały obejmują stopy takie jak 360, 380, 383 i 413.
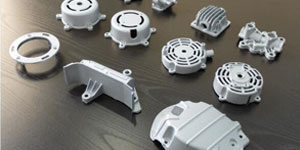
Pomoc w projektowaniu odlewów cynkowych/równoległe usługi inżynieryjne. Zleceniodawca precyzyjnych odlewów cynkowych. Można wytwarzać miniaturowe odlewy, odlewy ciśnieniowe wysokociśnieniowe, odlewy wielopłytkowe, konwencjonalne odlewy formowe, odlewy jednostkowe i niezależne oraz odlewy z uszczelnieniem gniazdowym. Odlewy mogą być produkowane w długościach i szerokościach do 24 cali z tolerancją +/- 0.0005 cala.
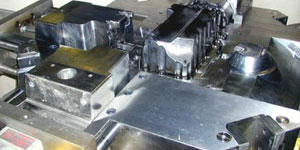
Certyfikowany ISO 9001: 2015 producent odlewanego magnezu, Możliwości obejmują odlewanie ciśnieniowe magnezu do 200 ton gorącej komory i 3000 ton zimnej komory, projektowanie oprzyrządowania, polerowanie, formowanie, obróbka skrawaniem, malowanie proszkowe i płynne, pełna kontrola jakości z możliwościami CMM , montaż, pakowanie i dostawa.
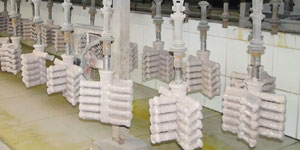
Certyfikat ITAF16949. Dodatkowa usługa odlewania obejmuje casting inwestycyjny,odlewanie piaskowe,Odlewanie grawitacyjne, Utracone odlewanie pianki,Odlewanie odśrodkowe,Odlewanie próżniowe,Trwałe odlewanie form,.Możliwości obejmują EDI, pomoc inżynierską, modelowanie bryłowe i przetwarzanie wtórne.
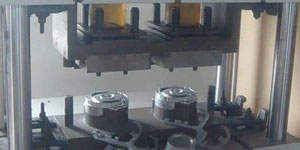
Przemysł odlewniczy Części Studia przypadków dla: samochodów, rowerów, samolotów, instrumentów muzycznych, jednostek pływających, urządzeń optycznych, czujników, modeli, urządzeń elektronicznych, obudów, zegarów, maszyn, silników, mebli, biżuterii, przyrządów, telekomunikacji, oświetlenia, urządzeń medycznych, urządzeń fotograficznych, Roboty, rzeźby, sprzęt dźwiękowy, sprzęt sportowy, narzędzia, zabawki i inne.
W czym możemy Ci pomóc dalej?
∇ Przejdź do strony głównej dla Odlewanie ciśnieniowe Chiny
→Części odlewnicze-Dowiedz się, co zrobiliśmy.
→Powiązane wskazówki dotyczące Usługi odlewania ciśnieniowego
By Producent odlewów ciśnieniowych Minghe |Kategorie: Przydatne artykuły |Materiał tagi: Odlewanie aluminium, Odlew cynkowy, Odlewanie magnezu, Casting tytanu, Odlewanie ze stali nierdzewnej, Odlew mosiężny,Odlew z brązu,Przesyłanie wideo,Historia firmy,Odlew aluminiowy |Komentarze wyłączone