7 FAQ w dziedzinie produkcji form
Jaki jest główny czynnik wpływający na skrawalność materiału?
Bardzo ważny jest skład chemiczny stali. Im wyższy skład stopowy stali, tym trudniej jest przetwarzać. Wraz ze wzrostem zawartości węgla spada wydajność skrawania metalu.
Struktura stali jest również bardzo ważna dla wydajności cięcia metalu. Różne struktury obejmują: kute, odlewane, wytłaczane, walcowane i obrabiane. Odkuwki i odlewy mają bardzo trudne do obróbki powierzchnie.
Twardość jest ważnym czynnikiem wpływającym na wydajność skrawania metalu. Ogólna zasada jest taka, że im twardsza stal, tym trudniej ją obrabiać. Stal szybkotnąca (HSS) może być używana do obróbki materiałów o twardości do 330-400HB; stal szybkotnąca + powłoka TiN może przetwarzać materiały o twardości do 45HRC; a dla materiałów o twardości 65-70HRC należy użyć węglika spiekanego, ceramiki, cermetali i regularnego azotku boru (CBN).
Wtrącenia niemetaliczne generalnie mają negatywny wpływ na trwałość narzędzia. Na przykład Al2O3 (tlenek glinu), który jest czystą ceramiką, jest wysoce ścierny.
Ostatnim z nich jest naprężenie szczątkowe, które może powodować problemy z wydajnością skrawania metalu. Często zaleca się wykonanie procesu odprężania po obróbce zgrubnej.
Jakie są właściwości skrawania żeliwa?
Ogólnie rzecz biorąc jest to:
Im wyższa twardość i wytrzymałość żeliwa, tym niższa wydajność skrawania metalu oraz niższa oczekiwana żywotność ostrzy i frezów. Większość rodzajów żeliwa wykorzystywanych do obróbki skrawaniem metali na ogół charakteryzuje się dobrą wydajnością skrawania metalu. Wydajność skrawania metalu jest powiązana ze strukturą, a twardsze żeliwo perlityczne jest również trudniejsze w obróbce. Żeliwo z grafitem płatkowym i żeliwo ciągliwe mają doskonałe właściwości skrawające, podczas gdy żeliwo sferoidalne jest dość złe.
Główne rodzaje zużycia spotykane podczas obróbki żeliwa to: zużycie ścierne, adhezyjne i dyfuzyjne. Ścieranie jest powodowane głównie przez węgliki, drobinki piasku i twarde odlewy. Zużycie spoiwa z narostem na krawędzi występuje przy niskiej temperaturze skrawania i przy niskiej prędkości skrawania. Ferrytowa część żeliwa jest najłatwiejsza do przyspawania do ostrza, ale można temu zaradzić, zwiększając prędkość i temperaturę cięcia.
Z drugiej strony zużycie dyfuzyjne jest zależne od temperatury i występuje przy dużych prędkościach skrawania, zwłaszcza w przypadku stosowania gatunków żeliwa o dużej wytrzymałości. Gatunki te mają wysoką odporność na odkształcenia, co prowadzi do wysokich temperatur. Zużycie to jest związane z interakcją między żeliwem a narzędziem skrawającym, co powoduje, że niektóre żeliwa wymagają obróbki przy dużych prędkościach za pomocą ceramicznych lub regularnych narzędzi skrawających z azotku boru (CBN), aby uzyskać dobrą trwałość i jakość powierzchni.
Generalnie typowymi właściwościami narzędzia wymaganymi do obróbki żeliwa są: wysoka twardość termiczna i stabilność chemiczna, ale ma to również związek z procesem, przedmiotem obrabianym i warunkami skrawania; krawędź tnąca musi mieć ciągliwość, odporność na zmęczenie cieplne i wytrzymałość krawędzi. Stopień zadowolenia z skrawania żeliwa zależy od tego, jak rozwija się zużycie krawędzi skrawającej: szybkie tępienie oznacza, że gorące pęknięcia i wyszczerbienia powodują przedwczesne pękanie krawędzi skrawającej, uszkodzenie przedmiotu obrabianego, słabą jakość powierzchni, nadmierną falistość itp. Normalne zużycie powierzchni przyłożenia , równowaga i ostre krawędzie skrawające są tym, co zwykle wymaga wysiłku.
Jakie są główne i powszechne procedury przetwarzania w produkcji form?
Proces cięcia należy podzielić na co najmniej 3 typy procesów:
Obróbka zgrubna, półwykańczająca i wykańczająca, a czasem nawet superwykańczająca (głównie zastosowania przy obróbce z dużą prędkością). Frezowanie resztkowe jest oczywiście przygotowane do wykańczania po procesie półwykańczającym. W każdym procesie należy dążyć do pozostawienia równomiernie rozłożonego marginesu na kolejny proces, co jest bardzo ważne. Jeśli kierunek i obciążenie ścieżki narzędzia rzadko zmieniają się gwałtownie, żywotność narzędzia może być wydłużona i bardziej przewidywalna. W miarę możliwości proces wykańczania należy przeprowadzić na dedykowanej obrabiarce. Poprawi to dokładność geometryczną i jakość formy przy krótszym czasie debugowania i montażu.
Jakie narzędzia powinny być używane w tych różnych procesach?
Proces obróbki zgrubnej: frez z okrągłym ostrzem, frez z kulką i frez z dużym promieniem łuku noskowego.
Obróbka półwykańczająca: frez tarczowy (frez tarczowy o zakresie średnic 10-25mm), frez kulisty.
Proces wykańczania: frez z okrągłym ostrzem, frez kulkowy.
Proces frezowania szczątkowego: frez tarczowy, frez kulkowy, frez pionowy.
Bardzo ważna jest optymalizacja procesu skrawania poprzez wybór kombinacji specjalnych rozmiarów narzędzi, geometrii i gatunków, a także parametrów skrawania i odpowiednich strategii frezowania.
Informacje na temat narzędzi o wysokiej produktywności, które można zastosować, można znaleźć w katalogu C-1102:1 dotyczącym produkcji form
Czy jest jeden z najważniejszych czynników w procesie cięcia?
Jednym z najważniejszych celów w procesie skrawania jest stworzenie równomiernie rozłożonego naddatku na obróbkę dla każdego narzędzia w każdym procesie. Oznacza to, że należy używać narzędzi o różnych średnicach (od dużych do małych), zwłaszcza w operacjach obróbki zgrubnej i półwykańczającej. Głównym kryterium w każdym momencie powinna być jak najbardziej zbliżona do ostatecznego kształtu formy w każdym procesie.
Zapewnienie równomiernie rozłożonych naddatków na obróbkę dla każdego narzędzia zapewnia stałą i wysoką produktywność oraz bezpieczny proces skrawania. Gdy ap/ae (osiowa głębokość skrawania/promieniowa głębokość skrawania) nie zmienia się, prędkość skrawania i prędkość posuwu mogą być również stale utrzymywane na wysokim poziomie. W ten sposób działania mechaniczne i zmiany obciążenia na krawędzi skrawającej są niewielkie, więc generowane ciepło i zmęczenie są również mniejsze, co zwiększa żywotność narzędzia. Jeżeli kolejne procesy są niektórymi procesami półwykańczającymi, zwłaszcza wszystkimi procesami wykańczającymi, można przeprowadzić obróbkę bezobsługową lub częściową obróbkę bezobsługową. Stały naddatek na obróbkę materiału jest również podstawowym standardem w zastosowaniach z dużą prędkością skrawania.
Kolejnym korzystnym efektem stałego naddatku na obróbkę jest niewielki niekorzystny wpływ na szyny prowadzące obrabiarki, śruby kulowe i łożyska wrzeciona.
Dlaczego frezy z ostrzami okrągłymi są najczęstszym wyborem do narzędzi do obróbki zgrubnej form?
Jeśli do zgrubnego frezowania wnęki używany jest frez czworokątny, duża ilość stopniowego naddatku na obróbkę zostanie usunięta podczas obróbki półwykańczającej. Zmieni to siłę skrawania i spowoduje wygięcie narzędzia. Rezultatem jest pozostawienie nierównego naddatku na obróbkę wykańczającą, co wpływa na dokładność geometryczną formy. Jeśli użyjesz frezu walcowo-czołowego (z trójkątną płytką) ze słabszym czubkiem, uzyska on nieprzewidywalne efekty skrawania. Płytki trójkątne lub diamentowe również wytwarzają większe promieniowe siły skrawania, a ponieważ liczba krawędzi skrawających płytek jest niewielka, są one mniej ekonomicznymi narzędziami do obróbki zgrubnej.
Z drugiej strony okrągłą wkładkę można frezować w różnych materiałach i we wszystkich kierunkach. Jeśli jest używany, przejście między sąsiednimi ścieżkami narzędzia jest płynniejsze, a także może pozostawić mniejszą i bardziej jednolitą obróbkę do półwykańczania. margines. Jedną z cech charakterystycznych ostrzy okrągłych jest to, że grubość wytwarzanych przez nie wiórów jest zmienna. Dzięki temu mogą stosować wyższe prędkości posuwu niż większość innych płytek.
Kąt przystawienia płytki okrągłej zmienia się od prawie zera (bardzo płytkie cięcie) do 90 stopni, a cięcie jest bardzo płynne. Przy maksymalnej głębokości skrawania kąt przystawienia wynosi 45 stopni. Przy cięciu wzdłuż prostej ściany z zewnętrznym okręgiem kąt przystawienia wynosi 90 stopni. Wyjaśnia to również, dlaczego wytrzymałość narzędzia z okrągłym ostrzem jest duża – obciążenie cięcia stopniowo wzrasta. Do obróbki zgrubnej i półzgrubnej należy zawsze używać jako pierwszego wyboru frezów z okrągłymi ostrzami, takich jak CoroMill200 (patrz katalog produkcji form C-1102:1). W obróbce 5-osiowej bardzo odpowiednie są płytki okrągłe, zwłaszcza że nie mają ograniczeń.
Dzięki dobremu programowaniu frezy na płytki okrągłe mogą w dużej mierze zastąpić frezy kulkowe. Okrągłe ostrze z małym biciem jest połączone z drobno szlifowanym, dodatnim kątem natarcia i lekką geometrią cięcia i może być również używane do półwykańczania i niektórych procesów wykończeniowych.
Jaka jest efektywna prędkość skrawania (ve) i dlaczego jest to zawsze bardzo ważne dla podstawowego obliczenia efektywnej prędkości skrawania na efektywnej średnicy wysokiej produktywności.
Ponieważ posuw stołu zależy od prędkości obrotowej przy określonej prędkości skrawania, jeśli prędkość efektywna nie zostanie obliczona, posuw stołu zostanie obliczony nieprawidłowo.
Jeżeli do obliczania prędkości skrawania używana jest średnica nominalna narzędzia (Dc), gdy głębokość skrawania jest niewielka, efektywna lub rzeczywista prędkość skrawania jest znacznie niższa niż prędkość obliczona. Takie jak narzędzia CoroMill200 z okrągłą płytką (zwłaszcza w zakresie małych średnic), frezy kulkowe, frezy walcowo-czołowe o dużym promieniu naroża i CoroMill390 oraz inne narzędzia (informacje o tych narzędziach można znaleźć w artykule dotyczącym produkcji form firmy Sandvik Coromant, próbka C-1102:1 ). W rezultacie obliczona prędkość posuwu jest również znacznie niższa, co znacznie zmniejsza wydajność. Co ważniejsze, warunki skrawania narzędzia są niższe niż jego możliwości i zalecany zakres zastosowań.
Proszę zachować źródło i adres tego artykułu do przedruku:7 FAQ w dziedzinie produkcji form
Minhe Firma odlewnicza są dedykowane do produkcji i zapewniania wysokiej jakości i wysokiej wydajności części odlewniczych (zakres części odlewanych z metalu obejmuje głównie) Cienkościenne odlewanie ciśnieniowe,Odlewanie pod ciśnieniem z komory gorącej,Odlewanie matrycowe w zimnej komorze), Usługa okrągła (usługa odlewania ciśnieniowego,Obróbka CNC,Produkcja form, Obróbka powierzchni). Wszelkie niestandardowe odlewanie ciśnieniowe z aluminium, odlewanie ciśnieniowe magnezu lub znalu / cynku oraz inne wymagania dotyczące odlewów są mile widziane, aby się z nami skontaktować.
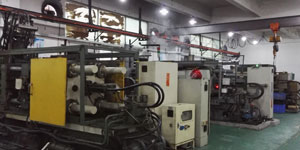
Pod kontrolą ISO9001 i TS 16949, wszystkie procesy są przeprowadzane przez setki zaawansowanych maszyn do odlewania ciśnieniowego, maszyn 5-osiowych i innych urządzeń, od blasterów po pralki Ultra Sonic. Minghe ma nie tylko zaawansowany sprzęt, ale także profesjonalny zespół doświadczonych inżynierów, operatorów i inspektorów, aby zrealizować projekt klienta.
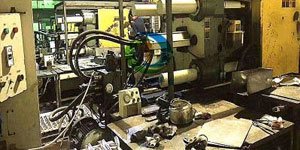
Producent kontraktowy odlewów ciśnieniowych. Możliwości obejmują odlewanie ciśnieniowe aluminium w zimnej komorze od 0.15 funta. do 6 funtów, szybka zmiana konfiguracji i obróbka. Usługi o wartości dodanej obejmują polerowanie, wibrowanie, gratowanie, śrutowanie, malowanie, powlekanie, powlekanie, montaż i oprzyrządowanie. Obrabiane materiały obejmują stopy takie jak 360, 380, 383 i 413.
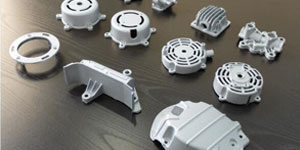
Pomoc w projektowaniu odlewów cynkowych/równoległe usługi inżynieryjne. Zleceniodawca precyzyjnych odlewów cynkowych. Można wytwarzać miniaturowe odlewy, odlewy ciśnieniowe wysokociśnieniowe, odlewy wielopłytkowe, konwencjonalne odlewy formowe, odlewy jednostkowe i niezależne oraz odlewy z uszczelnieniem gniazdowym. Odlewy mogą być produkowane w długościach i szerokościach do 24 cali z tolerancją +/- 0.0005 cala.
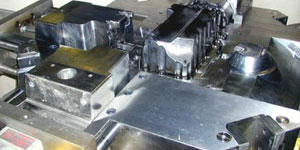
Certyfikowany ISO 9001: 2015 producent odlewanego magnezu, Możliwości obejmują odlewanie ciśnieniowe magnezu do 200 ton gorącej komory i 3000 ton zimnej komory, projektowanie oprzyrządowania, polerowanie, formowanie, obróbka skrawaniem, malowanie proszkowe i płynne, pełna kontrola jakości z możliwościami CMM , montaż, pakowanie i dostawa.
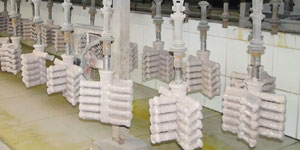
Certyfikat ITAF16949. Dodatkowa usługa odlewania obejmuje casting inwestycyjny,odlewanie piaskowe,Odlewanie grawitacyjne, Utracone odlewanie pianki,Odlewanie odśrodkowe,Odlewanie próżniowe,Trwałe odlewanie form,.Możliwości obejmują EDI, pomoc inżynierską, modelowanie bryłowe i przetwarzanie wtórne.
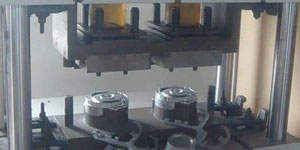
Przemysł odlewniczy Części Studia przypadków dla: samochodów, rowerów, samolotów, instrumentów muzycznych, jednostek pływających, urządzeń optycznych, czujników, modeli, urządzeń elektronicznych, obudów, zegarów, maszyn, silników, mebli, biżuterii, przyrządów, telekomunikacji, oświetlenia, urządzeń medycznych, urządzeń fotograficznych, Roboty, rzeźby, sprzęt dźwiękowy, sprzęt sportowy, narzędzia, zabawki i inne.
W czym możemy Ci pomóc dalej?
∇ Przejdź do strony głównej dla Odlewanie ciśnieniowe Chiny
→Części odlewnicze-Dowiedz się, co zrobiliśmy.
→Powiązane wskazówki dotyczące Usługi odlewania ciśnieniowego
By Producent odlewów ciśnieniowych Minghe |Kategorie: Przydatne artykuły |Materiał tagi: Odlewanie aluminium, Odlew cynkowy, Odlewanie magnezu, Casting tytanu, Odlewanie ze stali nierdzewnej, Odlew mosiężny,Odlew z brązu,Przesyłanie wideo,Historia firmy,Odlew aluminiowy |Komentarze wyłączone