Obróbka skrawaniem części metalurgii proszków (P/M)
Wykorzystanie procesu metalurgii proszków (P/M) do produkcji części do samochodowych systemów zasilania stale rośnie. Części produkowane metodą P/M mają wiele ważnych i unikalnych zalet. Pozostała porowata struktura celowo pozostawiona w tych częściach jest dobra dla samosmarowania i izolacji akustycznej. Złożone stopy, które są trudne lub niemożliwe do wytworzenia tradycyjnym procesem odlewania, można wytwarzać przy użyciu technologii P/M. Części wytwarzane w tej technologii zwykle mają niewielką lub żadną zdolność przerobową, co czyni je tańszymi i mniej odpadów materiałowych. Niestety, za atrakcyjnością tych cech, części P/M są trudne do obróbki.
Chociaż jednym z pierwotnych zamierzeń branży P/M jest wyeliminowanie wszelkiego przetwarzania, ten cel nie został jeszcze osiągnięty. Większość części może być tylko „zbliżona do ostatecznego kształtu” i nadal wymaga wykończenia.
Jednak w porównaniu z odlewami i odkuwkami, niewielka ilość materiału, który należy usunąć z części P/M, jest typowym materiałem odpornym na zużycie.
Porowata struktura to jedna z cech, które sprawiają, że części p/M mają szeroki zakres zastosowań, ale porowata struktura również ulegnie uszkodzeniu żywotności narzędzia. Porowata struktura może magazynować olej i dźwięk, ale prowadzi również do mikroprzerwanego cięcia. Podczas przemieszczania się tam iz powrotem od otworu do cząstek stałych, końcówka narzędzia jest stale uderzana, co może prowadzić do bardzo małych odkształceń pęknięć zmęczeniowych i drobnego zapadania się krawędzi wzdłuż krawędzi skrawającej. Co gorsza, cząsteczki są zwykle bardzo twarde. Nawet jeśli makrotwardość mierzonego materiału wynosi od 20 do 35 stopni, wielkość cząstek składnika wynosi aż 60 stopni. Te twarde cząstki powodują silne i szybkie zużycie krawędzi. Wiele części p / M można obrabiać cieplnie, a twardość i wytrzymałość materiału są wyższe po obróbce cieplnej. Wreszcie, ze względu na technologię spiekania i obróbki cieplnej oraz zastosowane gazy, powierzchnia materiału będzie zawierać twarde i odporne na zużycie tlenki i/lub węgliki.
Wydajność części P/M
Większość właściwości części P/M, w tym skrawalność, związana jest nie tylko ze składem chemicznym stopu, ale również z poziomem porowatości struktury porowatej. Porowatość wielu elementów konstrukcyjnych wynosi do 15% ~ 20%. Porowatość części wykorzystywanych jako urządzenia filtrujące może sięgać nawet 50%. Na drugim końcu serii porowatość części kutych lub biodrowych wynosi tylko 1% lub mniej. Materiały te stają się szczególnie ważne w zastosowaniach motoryzacyjnych i lotniczych, ponieważ mogą osiągać wyższy poziom wytrzymałości.
Wytrzymałość na rozciąganie, wiązkość i ciągliwość stopu P/M będzie wzrastać wraz ze wzrostem gęstości, a skrawalność również może ulec poprawie, ponieważ porowatość jest szkodliwa dla końcówki narzędzia.
Wzrost poziomu porowatości może poprawić izolacyjność akustyczną części. Drgania tłumiące w częściach standardowych są znacznie zredukowane w częściach P/M, co jest bardzo ważne w przypadku obrabiarek, dmuchaw klimatyzacji i narzędzi pneumatycznych. Wysoka porowatość jest również niezbędna w przypadku przekładni samosmarujących.
Trudności w obróbce
Chociaż jednym z celów ciągłego rozwoju branży P/M jest eliminacja obróbki skrawaniem, a jedną z głównych atrakcji procesu P/M jest to, że potrzebna jest tylko niewielka ilość obróbki, wiele części nadal wymaga dalszej obróbki w celu uzyskania wyższa dokładność lub lepsze wykończenie powierzchni. Niestety obróbka tych części jest niezwykle trudna. Większość napotykanych problemów jest spowodowana porowatością. Porowatość prowadzi do mikrozmęczenia krawędzi skrawającej. Ostrze stale wcina się i wycina. Przechodzi pomiędzy cząsteczkami i dziurami. Powtarzające się małe uderzenia prowadzą do małych pęknięć na krawędzi skrawającej.
Te pęknięcia zmęczeniowe narastają aż do zapadnięcia się krawędzi skrawającej. Ten rodzaj krawędzi mikrowykruszania jest zwykle bardzo mały i zwykle wykazuje normalne zużycie ścierne.
Porowatość zmniejsza również przewodność cieplną części P/M, co skutkuje wysoką temperaturą na krawędzi skrawającej oraz powoduje zużycie kraterowe i deformację. Wewnętrznie połączona porowata struktura zapewnia ścieżkę do odprowadzania płynu obróbkowego z obszaru skrawania. Może to powodować pęknięcia na gorąco lub deformację, zwłaszcza podczas wiercenia.
Zwiększenie pola powierzchni spowodowane wewnętrzną porowatą strukturą prowadzi również do utleniania i/lub karbonizacji podczas obróbki cieplnej. Jak wspomniano wcześniej, te tlenki i węgliki są twarde i odporne na zużycie.
Porowata struktura powoduje również niepowodzenie odczytu twardości części, co jest niezwykle ważne. Gdy celowo mierzy się makrotwardość części P / M, uwzględnia ona współczynnik twardości otworu. Porowata struktura prowadzi do zawalenia się struktury i daje mylne wrażenie stosunkowo miękkich części. Cząsteczki są znacznie twardsze. Jak opisano powyżej, różnica jest dramatyczna.
Niekorzystne jest również występowanie wtrąceń w częściach PM. Podczas obróbki cząstki te będą wyciągane z powierzchni, a rysa lub rysa powstaje na powierzchni części, gdy jest ona pocierana przed narzędziem. Wtrącenia te są zwykle duże, pozostawiając widoczne dziury na powierzchni części.
Różnica zawartości węgla prowadzi do niespójności obrabialności. Na przykład zawartość węgla w stopie fc0208 waha się od 0.6% do 0.9%. Partia materiałów o zawartości węgla 0.9% jest stosunkowo twarda, co skutkuje niską trwałością narzędzia. Druga partia materiałów o zawartości węgla 0.6% ma doskonałą trwałość. Oba stopy mieszczą się w dopuszczalnym zakresie.
Ostateczny problem obróbkowy związany jest z rodzajem skrawania, który występuje na części P/M. Ponieważ część jest zbliżona do ostatecznego kształtu, głębokość cięcia jest zwykle bardzo mała. Wymaga to swobodnej krawędzi tnącej. Nawarstwianie się wiórów na krawędzi skrawającej często prowadzi do mikroodprysków.
Technologia przetwarzania
Aby przezwyciężyć te problemy, stosuje się kilka technologii (unikalnych dla branży). Porowata struktura powierzchni jest często uszczelniana przez infiltrację. Zwykle wymagane jest dodatkowe cięcie swobodne. Ostatnio zastosowano ulepszone techniki produkcji proszków zaprojektowane w celu zwiększenia czystości proszków i redukcji tlenków i węglików podczas obróbki cieplnej.
Zamknięta porowata struktura powierzchni jest realizowana przez infiltrację metalem (zwykle miedzią) lub polimerem. Spekulowano, że infiltracja działa jak smar. Większość danych eksperymentalnych wskazuje, że prawdziwą zaletą jest zamknięcie porowatej struktury powierzchni, a tym samym zapobieganie mikrozmęczeniu krawędzi skrawającej. Redukcja drgań poprawia trwałość narzędzia i wykończenie powierzchni. Najbardziej dramatyczne zastosowanie infiltracji pokazuje 200% wzrost trwałości narzędzia, gdy porowata struktura jest zamknięta.
Wiadomo, że dodatki takie jak MNS, s, MoS2, MgSiO3 i BN zwiększają trwałość narzędzia. Dodatki te poprawiają skrawalność, ułatwiając oddzielenie wiórów od obrabianego przedmiotu, łamiąc wióry, zapobiegając ich gromadzeniu się i smarując krawędź skrawającą. Zwiększenie ilości dodatków może poprawić skrawalność, ale zmniejszyć wytrzymałość i wiązkość.
Technologia rozpylania proszku w celu kontrolowania gazu piecowego do spiekania i obróbki cieplnej umożliwia wytwarzanie czystego proszku i części, co minimalizuje występowanie wtrąceń i powierzchniowych węglików tlenkowych.
Materiał narzędzia
Najczęściej stosowanymi narzędziami w przemyśle P/M są te materiały, które są odporne na zużycie, pęknięcia krawędzi i wióry pod warunkiem dobrego wykończenia powierzchni. Te cechy są przydatne w każdej operacji obróbki, szczególnie w przypadku części P/M. Materiały narzędziowe zawarte w tej kategorii to narzędzia z regularnego azotku boru (CBN), niepowlekane i powlekane cermetale oraz ulepszone powlekane spiekane węgliki spiekane.
Narzędzia CBN są atrakcyjne ze względu na ich wysoką twardość i odporność na zużycie. Narzędzie to jest stosowane od wielu lat w obróbce stali i żeliwa o twardości Rockwella 45 i powyżej. Jednak ze względu na unikalne właściwości stopu P/M oraz znaczną różnicę między mikrotwardością a makrotwardością, narzędzia CBN mogą być stosowane do części P/M o twardości Rockwella 25. Kluczowym parametrem jest twardość cząstek. Gdy twardość cząstek przekracza Rockwella 50 stopni, narzędzia CBN są dostępne niezależnie od wartości makrotwardości. Oczywistym ograniczeniem tych narzędzi jest ich brak wytrzymałości. W przypadku przerywanego cięcia lub dużej porowatości konieczne jest wzmocnienie krawędzi, w tym ujemne fazowanie i ciężkie honowanie. Proste lekkie cięcie można wykonać za pomocą ostrzonej krawędzi tnącej.
Istnieje kilka skutecznych materiałów z CBN. Materiał o najlepszej ciągliwości składa się głównie z całego CBN. Mają doskonałą udarność, dzięki czemu można je stosować do obróbki zgrubnej. Ich ograniczenia są zwykle związane z wykończeniem powierzchni. Jest to w dużej mierze zdeterminowane przez poszczególne cząstki CBN, z których składa się narzędzie. Kiedy cząstki odpadną od krawędzi tnącej, będą miały wpływ na powierzchnię materiału obrabianego przedmiotu. Nie jest jednak tak poważne, że narzędzie do drobnych cząstek odpada z jednej cząstki.
Zwykle stosowany materiał CBN ma wysoką zawartość CBN i średnią wielkość cząstek. Ostrze wykańczające z CBN jest drobnoziarniste, a zawartość CBN jest niska. Są najskuteczniejsze, gdy wymagane jest lekkie cięcie i wykończenie powierzchni lub gdy obrabiany stop jest szczególnie twardy.
W wielu zastosowaniach skrawania trwałość narzędzia jest niezależna od rodzaju materiału. Innymi słowy, każdy materiał CBN może osiągnąć podobną trwałość narzędzia. W takich przypadkach wybór materiału opiera się głównie na najniższym koszcie każdej krawędzi skrawającej. Jedno okrągłe ostrze ma całą górną powierzchnię CBN i może zapewnić cztery lub więcej krawędzi tnących, co jest tańsze niż cztery inkrustowane ostrza CBN.
Gdy twardość części P / M jest niższa niż 35 stopni Rockwella, a twardość cząstek mieści się w zakresie, zwykle jednym z wyborów jest cermetal. Cermetale są bardzo twarde, mogą skutecznie zapobiegać gromadzeniu się wiórów i mogą wytrzymać duże prędkości. Ponadto, ponieważ cermetale zawsze były używane do szybkiej i wykańczającej obróbki stali i stali nierdzewnej, zwykle mają idealne rowki geometryczne odpowiednie dla części blisko formowanych.
Dzisiejsze cermetale są skomplikowane w metalurgii, zawierają do 11 pierwiastków stopowych. Są one zwykle spiekane z cząstek TiCN i kleju Ni Mo. TiCN zapewnia twardość, odporność na powstawanie wiórów i stabilność chemiczną, które są ważne dla pomyślnego stosowania cermetali. Ponadto narzędzia te mają zwykle wysoką zawartość kleju, co oznacza, że mają dobrą wytrzymałość. Jednym słowem, mają wszystkie cechy skutecznego przetwarzania stopu P / M. Kilka rodzajów cermetali jest skutecznych, podobnie jak węglik spiekany z węglika wolframu, im wyższa zawartość spoiwa, tym lepsza ciągliwość.
Znanym stosunkowo nowym zjawiskiem jest to, że chemiczne osadzanie z fazy gazowej w średniej temperaturze (mtcvd) zapewnia również korzyści dla przemysłu P/M. Mtcvd zachowuje całą odporność na zużycie i odporność na zużycie kraterowe tradycyjnego chemicznego osadzania z fazy gazowej (CVD), ale także obiektywnie poprawia wytrzymałość. Wzrost twardości wynika głównie ze zmniejszenia pęknięć. Powłoka jest osadzana w wysokiej temperaturze, a następnie chłodzona w piecu. Powłoka zawiera pęknięcia, gdy narzędzie osiąga temperaturę pokojową z powodu nierównomiernej rozszerzalności cieplnej. Podobnie jak rysy na płaskim szkle, pęknięcia te zmniejszają wytrzymałość krawędzi tnącej. Niższa temperatura osadzania mtcvd prowadzi do mniejszej częstotliwości pęknięć i lepszej udarności krawędzi skrawającej.
Gdy podłoże powłoki CVD i powłoki mtcvd mają te same właściwości i wykończenie krawędzi, można wykazać różnicę w ich wytrzymałości. W przypadku zastosowania w zastosowaniach, w których wymagana jest udarność krawędzi, wydajność powłoki mtcvd jest lepsza niż powłoki CVD. Poprzez analizę, podczas obróbki części P/M o porowatej strukturze, ważna jest udarność krawędzi. Powłoka Mtcvd jest lepsza niż powłoka CVD.
Powłoka fizycznego osadzania z fazy gazowej (PVD) jest cieńsza i mniej odporna na zużycie niż powłoka mtcvd lub CVD. Jednak powłoka PVD może wytrzymać znaczny wpływ podczas aplikacji. Powłoka PVD jest skuteczna, gdy cięcie powoduje zużycie ścierne, CBN i cermetale są zbyt kruche i wymagają doskonałego wykończenia powierzchni.
Na przykład krawędź skrawającą z węglika spiekanego C-2 można obrabiać fc0205 z prędkością liniową 180 m/min i posuwem 0.15 mm/obr. Po obróbce 20 części nagromadzenie wiórów może spowodować mikrozapadnięcie. W przypadku zastosowania powłoki z azotku tytanu PVD (TIN) odkładanie się wiórów jest ograniczone, a żywotność narzędzia wydłużona. Gdy w tym teście stosuje się powłokę cynową, oczekuje się, że charakterystyka zużycia ściernego części P / M będzie bardziej skuteczna w przypadku powłoki TiCN. TiCN ma prawie taką samą odporność na tworzenie się wiórów jak cyna, ale jest twardszy i bardziej odporny na zużycie niż cyna.
Struktura porowata jest ważna i wpływa na skrawalność stopu fc0208. Gdy zmienia się porowata struktura i właściwości, różne materiały narzędziowe zapewniają odpowiednie korzyści. Gdy gęstość jest niska (6.4 g/cm3), makrotwardość jest niska. W takim przypadku węglik spiekany powlekany mtcvd zapewnia najlepszą trwałość narzędzia. Bardzo ważne jest mikro zmęczenie krawędzi skrawającej, a wytrzymałość krawędzi jest bardzo ważna. W takim przypadku ostrze cermetalowe o dobrej udarności zapewnia maksymalną trwałość narzędzia.
Przy produkcji tego samego stopu o gęstości 6.8 g/cm3 zużycie ścierne staje się ważniejsze niż pękanie krawędzi. W takim przypadku powłoka mtcvd zapewnia najlepszą trwałość narzędzia. Węglik spiekany powlekany metodą PVD jest używany do testowania dwóch rodzajów wyjątkowo twardych części i pęka, gdy dotyka krawędzi skrawającej.
Gdy prędkość wzrasta (prędkość liniowa wynosi ponad 300 metrów na minutę), cermetale, a nawet cermetale powlekane, powodują zużycie kraterowe. Powlekany węglik spiekany jest bardziej odpowiedni, zwłaszcza gdy udarność ostrza powlekanego węglika spiekanego jest dobra. Powłoka Mtcvd jest szczególnie skuteczna w przypadku węglika spiekanego z obszarem bogatym w kobalt.
Cermetale są najczęściej używane do toczenia i wytaczania. Węgliki spiekane pokrywane metodą PVD są idealne do obróbki gwintów, ponieważ można oczekiwać niższych prędkości i większej uwagi na narastanie.
Proszę zachować źródło i adres tego artykułu do przedruku:Obróbka skrawaniem części metalurgii proszków (P/M)
Minghe Casting Company zajmuje się produkcją i dostarczaniem wysokiej jakości i wysokiej jakości części odlewniczych (zakres części odlewanych z metalu obejmuje głównie) Cienkościenne odlewanie ciśnieniowe,Odlewanie pod ciśnieniem z komory gorącej,Odlewanie matrycowe w zimnej komorze), Usługa okrągła (usługa odlewania ciśnieniowego,Obróbka CNC,Produkcja form, Obróbka powierzchni). Wszelkie niestandardowe odlewanie ciśnieniowe z aluminium, odlewanie ciśnieniowe magnezu lub znalu / cynku oraz inne wymagania dotyczące odlewów są mile widziane, aby się z nami skontaktować.
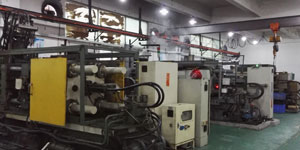
Pod kontrolą ISO9001 i TS 16949, wszystkie procesy są przeprowadzane przez setki zaawansowanych maszyn do odlewania ciśnieniowego, maszyn 5-osiowych i innych urządzeń, od blasterów po pralki Ultra Sonic. Minghe ma nie tylko zaawansowany sprzęt, ale także profesjonalny zespół doświadczonych inżynierów, operatorów i inspektorów, aby zrealizować projekt klienta.
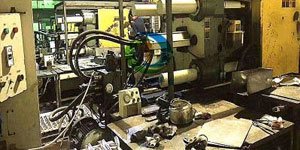
Producent kontraktowy odlewów ciśnieniowych. Możliwości obejmują odlewanie ciśnieniowe aluminium w zimnej komorze od 0.15 funta. do 6 funtów, szybka zmiana konfiguracji i obróbka. Usługi o wartości dodanej obejmują polerowanie, wibrowanie, gratowanie, śrutowanie, malowanie, powlekanie, powlekanie, montaż i oprzyrządowanie. Obrabiane materiały obejmują stopy takie jak 360, 380, 383 i 413.
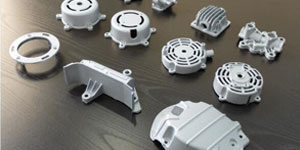
Pomoc w projektowaniu odlewów cynkowych/równoległe usługi inżynieryjne. Zleceniodawca precyzyjnych odlewów cynkowych. Można wytwarzać miniaturowe odlewy, odlewy ciśnieniowe wysokociśnieniowe, odlewy wielopłytkowe, konwencjonalne odlewy formowe, odlewy jednostkowe i niezależne oraz odlewy z uszczelnieniem gniazdowym. Odlewy mogą być produkowane w długościach i szerokościach do 24 cali z tolerancją +/- 0.0005 cala.
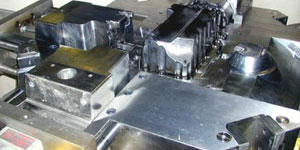
Certyfikowany ISO 9001: 2015 producent odlewanego magnezu, Możliwości obejmują odlewanie ciśnieniowe magnezu do 200 ton gorącej komory i 3000 ton zimnej komory, projektowanie oprzyrządowania, polerowanie, formowanie, obróbka skrawaniem, malowanie proszkowe i płynne, pełna kontrola jakości z możliwościami CMM , montaż, pakowanie i dostawa.
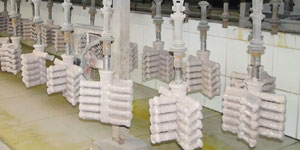
Certyfikat ITAF16949. Dodatkowa usługa odlewania obejmuje casting inwestycyjny,odlewanie piaskowe,Odlewanie grawitacyjne, Utracone odlewanie pianki,Odlewanie odśrodkowe,Odlewanie próżniowe,Trwałe odlewanie form,.Możliwości obejmują EDI, pomoc inżynierską, modelowanie bryłowe i przetwarzanie wtórne.
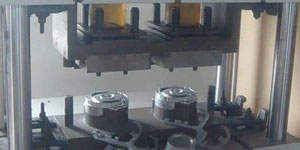
Przemysł odlewniczy Części Studia przypadków dla: samochodów, rowerów, samolotów, instrumentów muzycznych, jednostek pływających, urządzeń optycznych, czujników, modeli, urządzeń elektronicznych, obudów, zegarów, maszyn, silników, mebli, biżuterii, przyrządów, telekomunikacji, oświetlenia, urządzeń medycznych, urządzeń fotograficznych, Roboty, rzeźby, sprzęt dźwiękowy, sprzęt sportowy, narzędzia, zabawki i inne.
W czym możemy Ci pomóc dalej?
∇ Przejdź do strony głównej dla Odlewanie ciśnieniowe Chiny
→Części odlewnicze-Dowiedz się, co zrobiliśmy.
→Powiązane wskazówki dotyczące Usługi odlewania ciśnieniowego
By Producent odlewów ciśnieniowych Minghe |Kategorie: Przydatne artykuły |Materiał tagi: Odlewanie aluminium, Odlew cynkowy, Odlewanie magnezu, Casting tytanu, Odlewanie ze stali nierdzewnej, Odlew mosiężny,Odlew z brązu,Przesyłanie wideo,Historia firmy,Odlew aluminiowy |Komentarze wyłączone