Jak zapewnić stabilność systemu zielonego piasku?
I. Wstęp
Ze względu na zmiany warunków produkcji i otoczenia, inne parametry odlewu nieuchronnie ulegną zmianie. Jeśli procesu masy formierskiej nie można dostosować w czasie, system piasku będzie niestabilny, co ostatecznie doprowadzi do trudniejszego czyszczenia odlewu, a nawet złomu;
W ten sposób konieczne jest dostosowanie pierwotnego procesu mas formierskich w celu ustabilizowania systemu masowego; skład materiałowy mas formierskich składa się głównie ze starego piasku, piasku surowego, bentonitu i dodatków. Ponieważ ponad 95% masy formierskiej to stary piasek, a na stary piasek wpływają takie czynniki, jak różny stosunek piasku do żelaza w odlewie i różna ilość mieszania masy rdzeniowej, co powoduje bardzo duże wahania skład materiału. W związku z tym, aby kontrolować skład masy formierskiej, konieczne jest kontrolowanie zawartości efektywnej bentonitu, efektywnej zawartości dodatków oraz zawartości mułu w masie formierskiej w celu określenia ilości dodanej bentonitu, dodatków i masy surowej podczas mieszania masy.
W tym artykule pokrótce przedstawimy, w jaki sposób odlewnia firmy autora jest zakorzeniona w rzeczywistym procesie produkcyjnym.
Zgodnie ze zmianą parametrów proces mas formierskich jest dostosowywany, aby zapewnić stabilność systemu masowego.
2. Definicja kluczowych parametrów masy formierskiej:
1. Efektywna zawartość bentonitu: Efektywną zawartość bentonitu (aktywnego) określa się na podstawie właściwości zawartego w bentonicie minerału montmorylonitowego, który może absorbować błękit metylenowy i inne barwniki; dotyczy miareczkowania masy formierskiej 5.00 g czystym roztworem błękitu metylenowego o stężeniu 0.20% [mL]; przeliczona według wzoru krzywej standardowej bentonitu (%)
2. Efektywne dozowanie dodatków: Porównuje się je z wydzielaniem gazu dodatków do masy formierskiej i oblicza na podstawie wzoru; to znaczy wydzielanie gazu z 1.00 g masy formierskiej w temperaturze 900°C [ml] minus wydzielanie gazu aktywowanego bentonitu w masie formierskiej (średnia ilość zmierzona przed obliczeniami). Następnie porównaj z 1 g objętości gazu dodatku (%).
3. Zawartość błota: Zgodnie z krajową normą GB / T9442-1998 drobne cząstki proszku o średnicy mniejszej niż 20 μm są określane jako błoto. Osad usuwa się zwykle metodą płukania [2].
4. Wielkość cząstek masy formierskiej: wyrażona w miałkości AFS, czyli średnia wielkość cząstek piasku jest odzwierciedlona zgodnie z wyimaginowanym oznaczeniem sita [3];
5. Metoda obliczania próby AFS: Procedury pomiaru próby i metody obliczeniowe AFS określone przez American Institute of Foundry są następujące:
. Najpierw zważyć około 50g próbki piasku, zmyć błoto, osuszyć, a następnie przesiać
. Zważ i zanotuj jakość cząstek piasku pozostających na każdym sicie;
. Oblicz procentową ilość cząstek piasku pozostających na każdym sicie do całkowitej ilości próbek piasku;
. Pomnóż procentową ilość cząstek piasku pozostających na każdym sicie przez „mnożnik miałkości AFS” odpowiadający każdemu sicie;
. Dodaj powyższe produkty dla każdego numeru sita, aby znaleźć sumę:
. Podziel sumę uzyskaną w pozycji 5 przez sumę procentów piasku zatrzymanego na każdym sicie w pozycji 3, aby uzyskać miałkość AFS
3. Plan dostosowania:
Sprzęt do mieszania piasku używany przez fabrykę to młyn do piasku DISA i sprzęt do formowania KW ciśnieniowa linia do formowania statycznego; na podstawie statystyk danych z pół roku sformułowano następujące plany dla systemu mas formierskich:
1. Statystyki:
① Określ ilość piasku formierskiego dodawanego do każdego pudełka zgodnie z wartością ustawienia hosta formierskiego i oblicz stosunek piasku do żelaza każdego pudełka odlewów zgodnie z wagą każdego pudełka odlewów i wagą wylewania system i ilość piasku rdzeniowego użytego do odlewania;
②Statystyki ilości zrzucanego piasku odpadowego oraz zużycia piasku rdzeniowego i materiałów pomocniczych
③ Statystyka odpylania układu mas formierskich
2. Regulacja piasku:
① W zależności od sytuacji produkcyjnej, gdy odlew jest produkowany w sposób ciągły przez dwa lub więcej dni, dodana ilość akcesoriów do mas (bentonit, dodatki) powinna zostać ustalona, a zmiany w efektywnej ilości masy zostaną policzone, oraz następnie stopniowo weryfikowany podczas ciągłej produkcji innych odlewów Zależność między stosunkiem piasku do żelaza a dodaną ilością;
② Dostosowanie wielkości cząstek masy formierskiej: dostosować zgodnie ze średnią wartością sita 50/100 (piasek krzemionkowy o sicie 50/100, średnia wartość średniej miałkości wynosi 50 [4]), gdy AFS masy formierskiej jest mniejsza lub równa 50, dodając drobny piasek 70/140 lub drobniejszy nowy piasek 140/70 jest dostosowywany, dodaje się 30 kg-60 kg na młyn i analizuje się zmianę wielkości cząstek.
③ Regulacja zawartości błota w masach formierskich: analiza zmian zawartości błota w układzie mas formierskich poprzez statystykę dobowego odpylania;
Po czwarte, specyficzny proces dostosowania:
1. Statystyka stosunku piasku odlewniczego do żelaza:
(Uwaga: Ponieważ korpus cylindra X2B1 jest odlany z integralnym rdzeniem piaskowym, piasek formierski nie będzie spalany, więc ciężar zewnętrznego piasku formierskiego jest obliczany jako „0”)
2. Dostosuj efektywną ilość zgodnie ze stosunkiem piasku do żelaza odlewu. Stosunek piasku do żelaza bloku cylindrów 56D wynosi 6.57. Wśród powyższych odlewów stosunek piasku do żelaza jest najwyższy wśród odlewów bloku cylindrów. Dlatego najpierw testowany jest blok cylindrów 56D:
Gdy 56D produkowano przez trzy kolejne dni, ilość dodatku wynosiła 22 kg/młyn, a ilość dodatku gliny wynosiła 33 kg/młyn; efektywna ilość dodatków wzrosła z 4.55% do 5.03%; efektywna ilość glinki wzrosła z 6.56% do 7%; wzrost o około 0.5%; Oznacza to, że przy produkcji cylindra 56D dodawana ilość powinna być wyższa niż wartość bilansowa układu piaskowego;
Dzięki powyższej analizie danych ilość dodanych materiałów pomocniczych jest dostosowywana w następujący sposób:
1) Gdy cylinder jest odtwarzany, ilość dodatku jest dostosowywana do 19 kg/młyn, a gdy ilość dodatku gliny wynosi 26 kg/młyn, statystyki danych z trzech kolejnych dni pokazują, że efektywna ilość dodatków zmieniła się z 4.36% do 4.29% ; efektywna ilość gliny zmieniła się z 4.36% na 4.29%. 7.22% staje się 7.11%; efektywna ilość waha się o 0.1%; dlatego plan dostosowania procesu jest rozsądny i może zapewnić równowagę systemu masy formierskiej;
2) Podobnie zależność pomiędzy ilością materiałów pomocniczych dodanych do innych odlewów a ilością efektywną oblicza się na podstawie analizy danych doświadczalnych i teorii; przy odtwarzaniu różnych odlewów należy dostosować odpowiednią ilość dodanych materiałów pomocniczych.
3. Użyj nowego piasku 70/140 mesh i nowego piasku 140/70, aby dostosować rozmiar piasku (zawartość błota w piasku prototypowym wynosi 11.42%):
① Od 16 stycznia do 21 stycznia łącznie 4257 razy mielenie piasku w ciągu pięciu dni, około 4257*3/900=14 razy; wielkość cząstek w każdym cyklu zmienia się o około 0.26 (na mielenie); dlatego masa formierska 16 stycznia Wartość AFS wynosi 49.15; od 16 stycznia przez pięć dni ciągłego dodawania 70/140 nowego piasku w celu dostosowania wielkości cząstek, 60 kg na młyn, wartość AFS dla masy formierskiej 21 stycznia wynosi 52.84;
② Od 25 stycznia do 27 stycznia łącznie 2165 razy mielenia piasku w ciągu trzech dni, około 2165*3/900=7 cykli; wielkość ziarna w każdym cyklu zmienia się o około 0.22 (na mielenie); dlatego 24 stycznia piasek AFS =52.44, kiedy wielkość cząstek piasku formierskiego osiąga 52-53, ciągłe dodawanie 70/140 nowego piasku ma niewielki wpływ na system piasku AFS; począwszy od 26 stycznia, 140/70 nowego piasku jest dodawane przez trzy kolejne dni w celu dostosowania, a 60 kg jest dodawane na każde zmielenie. 1 28-go AFS piasku wynosi 54.
(Uwaga: ①Standard przedsiębiorstwa FAW stanowi, że wskaźnik przesiewania piasku kwarcowego 70/140 70,100,140 80 70,100 ≥ 60%, z czego przesiewanie 140 70 ≥ 70,100,140%; piasek kwarcowy 80/100,140 60 3 900 wskaźnik przesiewania ≥ XNUMX%, z czego wskaźnik przesiewania XNUMX XNUMX ≥ XNUMX % ②Każda objętość mielenia wynosi XNUMX tony, a objętość piasku w systemie szacuje się na XNUMX ton)
4. Porównanie zawartości błota i odpylania przez trzy kolejne miesiące:
Ze względu na zimny klimat na północy od lutego do marca pył w rurociągu odpylania zimnego będzie się skraplać i krzepnąć po usunięciu pyłu gorącego. Jeśli rurociąg nie zostanie oczyszczony na czas, często będą występować zatory, a dzienny zrzut będzie wahał się od 4 do 8 ton. Zawartość błota w systemie piaskowym jest bardzo zróżnicowana. W tym okresie jedynym sposobem na zwiększenie wydajności odpylania i zmniejszenie zawartości błota jest zwiększenie objętości powietrza w sprzęcie odpylającym i pogłębianie rur;
Po wejściu kwietnia temperatura stopniowo wzrastała, zjawisko kondensacji i krzepnięcia pyłu przestało się pojawiać, ilość odpylania stopniowo ustabilizowała się, osiągając średni zrzut 7-8 ton na dobę, a zakres wahań zawartości mułu uległ zmniejszeniu;
Zawartość szlamu w systemie mas formierskich można również zmniejszyć poprzez dodanie nowego piasku lub ograniczenie dodawania materiałów pomocniczych. Wady tych dwóch metod zostaną wyjaśnione w podsumowaniu testu.
5. Wniosek z testu
1. Dostosuj efektywną ilość akcesoriów do piasku
Kryształy bentonitu są do pewnego stopnia uszkadzane przez ogrzewanie, a siła wiązania na mokro oczywiście zmniejszy się po dodaniu wody i wymieszaniu. Po wygrzaniu w wyższej temperaturze i dłuższym czasie struktura krystaliczna bentonitu ulega całkowitemu zniszczeniu, stając się „martwą gliną” bez siły spójności. Zwiększona grubość odlewu, niski stosunek piasku do żelaza, wysoka temperatura odlewania i długi czas chłodzenia zwiększają straty bentonitu podczas spalania.
Najbardziej bezpośrednią metodą oceny, czy skuteczny proszek węglowy w masie formierskiej jest wystarczający, jest obserwacja gładkości powierzchni odlewu i przywierania piasku. Część węgla w starym piasku jest spalana pod wpływem ciepła roztopionego metalu i wymaga uzupełnienia. Z drugiej strony, aby osiągnąć poziom efektywnego pyłu węglowego, należy również dodać nowe materiały, takie jak świeży piasek, mieszany piasek rdzeniowy i bentonit. Całkowita ilość pyłu węglowego dodanego podczas mieszania piasku jest sumą strat spalania i dodatkowej ilości uzupełniającej. (Efektywny proszek węglowy jest odpowiednikiem skutecznego dodatku w tekście)
2. Regulacja wielkości piasku:
Rozmiar cząstek masy formierskiej pod wysokim ciśnieniem wynosi na ogół 50/140, podczas gdy rozmiar cząstek rdzeni z masy żywicznej wynosi zwykle 50/100 lub więcej. Nadmierne mieszanie piasku rdzeniowego wpłynie na pogrubienie całego starego mokrego piasku, co zwiększy przepuszczalność piasku i szorstkość powierzchni odlewu.
Aby zapobiec zgrubieniu cząstek piasku formierskiego, cząstki z systemu odpylania można zawrócić do starego piasku. Lub dodaj drobny nowy piasek, aby dostosować; jak wspomniano w odlewni, gdy AFS masy formierskiej osiągnie około 48, należy regulować przez ciągłe dodawanie 70/140 lub 140/70 nowego piasku; jednak, ponieważ odlewy są włamywane do rdzenia układu piaskowego. Ilość piasku jest już duża. Jeżeli wielkość cząstek masy nie jest rozdrobniona w stopniu nie do zniesienia, nie zaleca się ciągłego dodawania tak dużej ilości nowej masy, w przeciwnym razie wpłynie to na inne wskaźniki wydajności systemu mas (zawartość błota, efektywna ilość i wytrzymałość ze względu na nadmierną ilość nowego piasku). )wpływać na;
3. Dostosowanie zawartości błota
Wzrost zawartości szlamu spowoduje zmniejszenie przepuszczalności masy formierskiej, a podczas procesu odlewania wystąpi zjawisko „wybuchu gazu”, a odlew zostanie złomowany w wyniku eksplozji i lepkiej masy. Zawartość błota w systemie mas formierskich nie powinna być zbyt wysoka; zawartość błota w układzie piaskowym można zmniejszyć poprzez zmniejszenie ilości materiałów pomocniczych, ale zmniejszenie efektywnej zawartości bentonitu spowoduje zmniejszenie wytrzymałości masy formierskiej, a także zmniejszy się zdolność do podnoszenia i opierania się piasku; skuteczne dozowanie Zmniejszenia spowoduje zmniejszenie zdolności antyadhezyjnej masy formierskiej.
Jeśli zwiększysz ilość dodawanego nowego piasku, aby dostosować zawartość błota, najpierw oblicz, ile błota wytwarzają różne nowo dodane materiały w piasku odlewanym, a następnie możesz obliczyć, ile surowego piasku należy dodać, aby zawartość błota masa formierska spełnia wymagania przepisów procesowych.
Jak wspomniano w artykule, zawartość błota można zmniejszyć o 0.1% na każde 30 kg nowego piasku dodawanego do odlewni; jednak nadmierne dodawanie nowego piasku nie tylko spowoduje stratę kosztów, ale także zmniejszy udział piasku używanego w układzie masy formierskiej, co zmniejszy wydajność masy formierskiej. , Masa formierska jest rozbieżna, co wpływa na zdolność masy formierskiej do formowania, a zjawisko wymywania masy występuje podczas procesu odlewania;
Dlatego autor uważa, że najlepszym wyborem jest kontrolowanie zawartości błota w układzie piaskowym poprzez regulację urządzeń odpylających.
Podsumowując, system stabilizowanego piasku ma być w stanie produkować wysokiej jakości odlewy. Dzięki tej koncepcji musimy stale dostosowywać proces mas formierskich do zmieniających się warunków produkcji, aby sprostać potrzebom produkcyjnym.
Proszę zachować źródło i adres tego artykułu do przedruku: Jak zapewnić stabilność systemu zielonego piasku?
Minhe Firma odlewnicza są dedykowane do produkcji i zapewniania wysokiej jakości i wysokiej wydajności części odlewniczych (zakres części odlewanych z metalu obejmuje głównie) Cienkościenne odlewanie ciśnieniowe,Odlewanie pod ciśnieniem z komory gorącej,Odlewanie matrycowe w zimnej komorze), Usługa okrągła (usługa odlewania ciśnieniowego,Obróbka CNC,Produkcja form, Obróbka powierzchni). Wszelkie niestandardowe odlewanie ciśnieniowe z aluminium, odlewanie ciśnieniowe magnezu lub znalu / cynku oraz inne wymagania dotyczące odlewów są mile widziane, aby się z nami skontaktować.
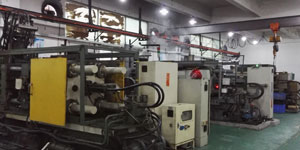
Pod kontrolą ISO9001 i TS 16949, wszystkie procesy są przeprowadzane przez setki zaawansowanych maszyn do odlewania ciśnieniowego, maszyn 5-osiowych i innych urządzeń, od blasterów po pralki Ultra Sonic. Minghe ma nie tylko zaawansowany sprzęt, ale także profesjonalny zespół doświadczonych inżynierów, operatorów i inspektorów, aby zrealizować projekt klienta.
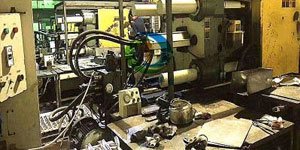
Producent kontraktowy odlewów ciśnieniowych. Możliwości obejmują odlewanie ciśnieniowe aluminium w zimnej komorze od 0.15 funta. do 6 funtów, szybka zmiana konfiguracji i obróbka. Usługi o wartości dodanej obejmują polerowanie, wibrowanie, gratowanie, śrutowanie, malowanie, powlekanie, powlekanie, montaż i oprzyrządowanie. Obrabiane materiały obejmują stopy takie jak 360, 380, 383 i 413.
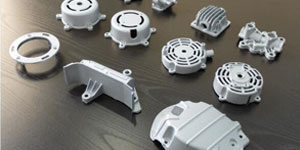
Pomoc w projektowaniu odlewów cynkowych/równoległe usługi inżynieryjne. Zleceniodawca precyzyjnych odlewów cynkowych. Można wytwarzać miniaturowe odlewy, odlewy ciśnieniowe wysokociśnieniowe, odlewy wielopłytkowe, konwencjonalne odlewy formowe, odlewy jednostkowe i niezależne oraz odlewy z uszczelnieniem gniazdowym. Odlewy mogą być produkowane w długościach i szerokościach do 24 cali z tolerancją +/- 0.0005 cala.
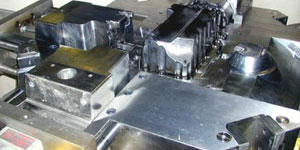
Certyfikowany ISO 9001: 2015 producent odlewanego magnezu, Możliwości obejmują odlewanie ciśnieniowe magnezu do 200 ton gorącej komory i 3000 ton zimnej komory, projektowanie oprzyrządowania, polerowanie, formowanie, obróbka skrawaniem, malowanie proszkowe i płynne, pełna kontrola jakości z możliwościami CMM , montaż, pakowanie i dostawa.
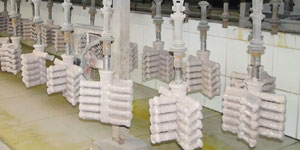
Certyfikat ITAF16949. Dodatkowa usługa odlewania obejmuje casting inwestycyjny,odlewanie piaskowe,Odlewanie grawitacyjne, Utracone odlewanie pianki,Odlewanie odśrodkowe,Odlewanie próżniowe,Trwałe odlewanie form,.Możliwości obejmują EDI, pomoc inżynierską, modelowanie bryłowe i przetwarzanie wtórne.
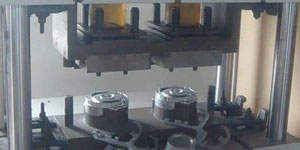
Przemysł odlewniczy Części Studia przypadków dla: samochodów, rowerów, samolotów, instrumentów muzycznych, jednostek pływających, urządzeń optycznych, czujników, modeli, urządzeń elektronicznych, obudów, zegarów, maszyn, silników, mebli, biżuterii, przyrządów, telekomunikacji, oświetlenia, urządzeń medycznych, urządzeń fotograficznych, Roboty, rzeźby, sprzęt dźwiękowy, sprzęt sportowy, narzędzia, zabawki i inne.
W czym możemy Ci pomóc dalej?
∇ Przejdź do strony głównej dla Odlewanie ciśnieniowe Chiny
→Części odlewnicze-Dowiedz się, co zrobiliśmy.
→Powiązane wskazówki dotyczące Usługi odlewania ciśnieniowego
By Producent odlewów ciśnieniowych Minghe |Kategorie: Przydatne artykuły |Materiał tagi: Odlewanie aluminium, Odlew cynkowy, Odlewanie magnezu, Casting tytanu, Odlewanie ze stali nierdzewnej, Odlew mosiężny,Odlew z brązu,Przesyłanie wideo,Historia firmy,Odlew aluminiowy |Komentarze wyłączone