Zastosowanie technologii impregnacji w produkcji silników
Impregnacja części wykonanych z lekkich materiałów, takich jak cylindry aluminiowe, może skutecznie zmniejszyć ilość odpadów obrabianych i znacznie poprawić ich jakość. Opierając się na założeniu zapewnienia jakości produktu, mogą skutecznie obniżyć koszty produkcji i poprawić wydajność produkcji.
Propozycja lekkiej i impregnacyjnej obróbki silnika
Lekkość stała się trendem we współczesnym przemyśle motoryzacyjnym, który jest determinowany głównie przez światową dbałość o ochronę środowiska i oszczędzanie energii. Z danych wynika, że jeśli masa własna samochodu zostanie zmniejszona o 10%, jego zużycie paliwa może wzrosnąć o 15%. Wzrost efektywności paliwowej oznacza zmniejszenie zużycia paliwa i emisji spalin. Dlatego zmniejszenie masy samochodu jest najskuteczniejszym sposobem poprawy oszczędności energii i ochrony środowiska samochodu. Silnik to najważniejszy duży zespół w samochodzie, a zmniejszenie jego masy ma kluczowe znaczenie dla zmniejszenia masy samochodu.
Z technicznego punktu widzenia istnieje wiele sposobów na osiągnięcie lekkości, takich jak optymalizacja całej konstrukcji maszyny, moduły akcesoriów i lekkość, ale wykorzystanie lekkich materiałów, takich jak tworzywa sztuczne, stopy aluminium i stopy magnezu w celu zastąpienia tradycyjnych materiałów, takich jak jak żeliwo to redukcja prądu. Główny sposób masy silnika. W rzeczywistości stop aluminium jest od wielu lat szeroko stosowany w głowicach cylindrów silnika, kolektorach dolotowych i mniejszych częściach, takich jak obudowy pomp wodnych i obudowy pomp olejowych, a coraz więcej firm stosuje bloki cylindrów ze stopu aluminium w ciągu ostatniej dekady. Jednak w porównaniu z żeliwem odlewy aluminiowe są bardziej podatne na wewnętrzne luzy, skurcz i pory podczas procesu odlewania z powodu tworzenia się kryształów, skurczu i absorpcji gazu. Te wadliwe odlewy mają gęstą warstwę powierzchniową po obróbce skrawaniem. Obszar jest usuwany, odsłaniając tym samym wewnętrzne wady organizacyjne. W przypadku tych odlewów aluminiowych, które wymagają szczelności w silniku, podczas przechodzenia przez proces wykrywania nieszczelności na linii produkcyjnej, istnienie wadliwych mikroporów spowoduje nadmierny wyciek i powstanie produktów odpadowych, czasami nawet w partiach. Ponieważ te warunki można wykryć dopiero po wielokrotnej obróbce, spowoduje to również poważne marnotrawstwo roboczogodzin, surowców i energii. Można zauważyć, że w celu rozwiązania problemu dużej ilości złomu odlewów aluminiowych, należy podjąć pewne środki obróbki w produkcji. Obecnie najczęściej stosowaną technologią jest impregnacja, czyli zatykanie przecieków. Tak zwana „impregnacja” polega na infiltracji infiltratora w mikropory odlewu aluminiowego w określonych warunkach, a po zestaleniu wypełniacz infiltrowany w por i wewnętrzną ściankę poru odlewu łączy się w całości z blokować mikropory, aby części mogły spełnić wymagania technologii procesowej wymaganej do zwiększania ciśnienia, zapobiegania przeciekaniu i zapobiegania wyciekom.
Proces impregnacji próżniowo-ciśnieniowej
Obecnie w produkcji odlewów aluminiowych w kraju i za granicą powszechnie stosuje się metodę infiltracji próżniowo-ciśnieniowej. Proces ten odbywa się głównie w zbiorniku próżniowym. W zależności od przebiegu procesu można go podzielić na trzy etapy: obróbka wstępna, obróbka impregnacyjna i obróbka końcowa. Jego różne etapy obejmują głównie: obróbka wstępna nazywana również obróbką wstępną mikroporowatą, która polega głównie na odtłuszczaniu, czyszczeniu i suszeniu odlewów w celu przygotowania do następnego procesu; pierwszym etapem obróbki impregnacyjnej jest umieszczenie detalu w koszu Następnie kosz włożyć do zbiornika impregnacyjnego; odkurzyć zbiornik impregnacyjny, aby usunąć gaz z porów części; przetransportować szczeliwo ze zbiornika magazynowego do zbiornika impregnacyjnego i zanurzyć części, które wciąż znajdują się pod próżnią; Ponownie odkurz zbiornik impregnacyjny, aby usunąć gaz ze szczeliwa; zwolnij próżnię i zwiększ ciśnienie w zbiorniku impregnacyjnym sprężonym powietrzem, co pomaga wcisnąć szczeliwo w pory; zwolnij ciśnienie i zwróć szczeliwo do zbiornika magazynowego; Obróbka końcowa polega głównie na usunięciu części, wirowaniu, płukaniu i zakończeniu operacji utwardzania.
Głównym celem obróbki wstępnej jest usunięcie plam olejowych, wiórów metalowych i kurzu z powierzchni części, poprawa jakości impregnacji oraz zapobieganie przedostawaniu się oleju i zanieczyszczeń mechanicznych do cieczy impregnacyjnej w celu wpłynięcia na penetrację i przyczepność. Powszechnie stosowane metody odtłuszczania obejmują odtłuszczanie rozpuszczalnikowe, odtłuszczanie ługiem i odtłuszczanie elektrochemiczne. Odlewy wyjmowane są po w/w odtłuszczeniu i oczyszczeniu, płukane gorącą wodą a następnie suszone w temp. 80-90℃. Aby poprawić efekt namaczania i zapobiec przedostawaniu się dużej ilości wody do pompy próżniowej, bardzo ważne jest suszenie po czyszczeniu.
Obróbka impregnacyjna polega na umieszczeniu wstępnie obrobionych detali w zbiorniku impregnacyjnym w celu uszczelnienia i odkurzenia, całkowitego usunięcia powietrza i drobnego pyłu ze zbiornika i porów odlewu oraz stworzenia warunków dynamicznych różnicy ciśnień dla napełniania i infiltracji środka impregnującego. Następnie infiltrant jest zasysany przez podciśnienie w zbiorniku i ponownie zasysane jest podciśnienie. Celem drugiego odkurzania jest odprowadzenie gazu z cieczy impregnacyjnej w zbiorniku, aby zapobiec przenikaniu cieczy impregnacyjnej zawierającej gaz do defektów mikroporów odlewu, tak aby uniknąć tworzenia się porów podczas krzepnięcia, które wpływają na uszczelnienie występ. Na koniec zwiększ ciśnienie, aby infiltrator, który został wypełniony i przeniknięty do porów odlewu, dalej wnikał do najgłębszej części każdej części ubytku. Impregnat jest płynną substancją sporządzoną z substancji nieorganicznych lub organicznych. Obecnie najszerzej stosowane szczeliwo metakrylanowe PC504/66 jest utwardzane pod wpływem ogrzewania i zapewnia wyraźne wypełnienie mikroporów przy niskim skurczu podczas polimeryzacji. Zdolność, w tym samym czasie, jego niska lepkość pomaga uszczelniaczowi szybko i głęboko wnikać w mikropory. Utwardzony uszczelniacz może normalnie funkcjonować w zakresie -50~200℃.
Obróbka końcowa polega na ociekaniu przedmiotu obrabianego, oczyszczeniu go i umieszczeniu w piecu do utwardzania w celu zestalenia, tak aby infiltrat wchodzący do porów odlewu zmienił się z ciekłego w stały, tworząc stałą zestaloną błonę. Temperatura utwardzania jest zwykle ustawiona na 80~90 ℃ lub umieszczona w temperaturze pokojowej (powyżej 25 ℃) na 24 godziny. Jeżeli odlew jest eksploatowany w temperaturze powyżej 300 ℃, należy go utwardzać w temperaturze 80 ℃ przez 2 godziny, a następnie w temperaturze 110 ℃ przez 1 godzinę.
Co do tego, która część procesu produkcyjnego jest impregnowana, różne zakłady produkcyjne i różne rodzaje detali są bardzo różne. Niewielka liczba firm ustanowi jednolite przepisy dla wszystkich części układu napędowego, które wymagają wysokiej dokładności wykonania i szczelności: takie części muszą być impregnowane przed obróbką, to znaczy, gdy są jeszcze w stanie odlewania, w celu osiągnięcia poprawy. Celem wykonania odlewu, wydłużeniem żywotności narzędzia podczas obróbki i zapewnieniem jakości produktu. Jednak większość fabryk nadal stosuje różne metody w zależności od różnych typów części. Ogólnie rzecz biorąc, w przypadku kilku kluczowych części, takich jak aluminiowy blok cylindrów w silniku, zwykle wymagane jest zaimpregnowanie wszystkich części w stanie odlewania, a następnie wysłanie ich. OEM. Jeśli chodzi o impregnację niektórych przedmiotów według określonych kryteriów po pewnym procesie na linii produkcyjnej OEM, zależy to od procesu produkcyjnego OEM.
W przypadku większości części generalnie nie wymaga się ich impregnowania, gdy znajdują się w stanie odlewów. Zamiast tego proces impregnacji jest wdrażany po pewnym procesie w procesie produkcyjnym, zgodnie z faktyczną sytuacją. Oznacza to, że gdy części po kilku procesach obróbki potwierdzą, że wartość wykrywania nieszczelności niektórych części mieści się w określonym przedziale, tylko ta część odrzuconego przedmiotu jest impregnowana. W większości przypadków odsetek odrzuconych elementów jest bardzo niski (około 1% do 2%), ale gdy ten odsetek przekroczy pewien limit (w zależności od konkretnej sytuacji), OEM będzie wymagać od fabryki półfabrykatów, aby Wszystkie odlewy były impregnowane .
Niektóre części, które wymagają impregnacji, nie są uwzględniane w procesie produkcyjnym OEM ze względów konstrukcyjnych. W przypadku części, których wyniki wykrywania nieszczelności są poza tolerancją, bez względu na to, jak duża jest rzeczywista zmierzona wartość, zostaną one bezpośrednio złomowane. Jeśli jednak wartość przecieku w pewnym stopniu przekroczy proporcję obrabianego przedmiotu, główna fabryka silników postawi również wymóg impregnacji dla wszystkich półfabrykatów odlewniczych.
A więc gdzie właściwie przebiega zabieg impregnacji? Powszechną praktykę w kraju i za granicą podejmują niezależne i profesjonalne przedsiębiorstwa. Jest to nie tylko wydajne i łatwe w zapewnieniu jakości, ale również koszt zakładu montażowego jest stosunkowo niski. Istnieje jednak również kilka fabryk silników z dużymi partiami, szybkim tempem produkcji i wysokimi wymaganiami jakościowymi produktów. Otworzą zamkniętą przestrzeń w warsztacie, dzięki czemu wyżej wymienione profesjonalne zakłady zajmujące się impregnacją będą mogły zbudować w miarę jednolitą, wydajną i wydajną linię do produkcji impregnatów o wyższym stopniu mechanizacji odpowiada wycinkowi warsztatu. Oczywiście tempo pracy tej „sekcji roboczej” jest niższe niż w przypadku ogólnej linii produkcyjnej.
Wykonaj wiele definicji impregnowanych przedmiotów
Jak wszyscy wiemy, jako główny korpus silnika, blok cylindrów jest wśród nich największą i najcięższą częścią. Przy wyborze stopu aluminium jego zmniejszenie masy o około połowę ma największe znaczenie dla lekkości silnika. Jednak ze względu na złożoną budowę bloku cylindrów i liczbę procesów obróbczych, w porównaniu z innymi odlewami aluminiowymi w silniku, prawdopodobieństwo wystąpienia wad wewnętrznych w bloku cylindrów aluminiowych podczas procesu odlewania i formowania jest również większe. W związku z tym, jak ujednolicić i skutecznie zastosować proces infiltracji immersji, aby zapewnić jego jakość, jest również najbardziej zaniepokojony przez przedsiębiorstwa. Poniżej, na przykładzie cylindra aluminiowego, problem definiowania i zatwierdzania przedmiotów obrabianych, które muszą być impregnowane, jest dalej wyjaśniony w reprezentatywnym przypadku. Nowo wybudowana linia produkcyjna do obróbki cylindrów aluminiowych w nowoczesnej fabryce silników samochodowych zakończyła wszystkie procesy obróbki zgrubnej przed wprowadzeniem przedmiotu na pośrednią stację mycia. Przed kolejnym montażem pokrywy łożyska głównego i kolejnymi operacjami wykończeniowymi ustawiono stanowisko do prób szczelności. Oprócz wykrywania nieszczelności niskociśnieniowego kanału olejowego, kanału wodnego i wysokociśnieniowego kanału olejowego aluminiowego bloku cylindrów, stacja ta jest również równoważna ustawieniu bramy. Zgodnie ze zmierzoną wartością przecieku, należy określić, czy ten aluminiowy cylinder jest impregnowany.
Dla przedmiotu obrabianego są ustawione dwa limity przesiewania: pierwszy to szybkość wycieku kontrolowanej części, na przykładzie kanału oleju pod niskim ciśnieniem, limit szybkości wycieku wynosi 30 CC/min; Druga granica przesiewania to Ta kontrolowana część ma na celu ustalenie, czy występuje przeciek w aluminiowej butli, ale czy jest możliwe i konieczne usunięcie go poprzez impregnację. Na przykładzie niskociśnieniowego kanału olejowego z tabeli wynika, że wynosi on 500 CC/min. W związku z tym, gdy aluminiowy korpus cylindra po procesie czyszczenia pośredniego wchodzi na stanowisko badania szczelności wzdłuż bieżni przenośnika, jeśli którakolwiek ze zmierzonych wartości nieszczelności przedmiotu obrabianego jest niższa niż odpowiadająca jej granica przesiewania podana w tabeli, to Oznacza to, że szybkość wycieku zostanie oceniona jako kwalifikowana, a następnie przejdzie do następnego procesu. Ale tak długo, jak którakolwiek z rzeczywistych zmierzonych wartości wycieków przekracza wskaźnik wycieku, ale jest mniejsza niż limit złomu, weź jako przykład przepływ oleju pod niskim ciśnieniem w tabeli, zakres wynosi od 30 do 500CC/min. Aluminiowy blok cylindrów jest traktowany jako przedmiot obrabiany, który należy wyjąć do impregnacji, wysłać bieżnią w odwrotnym kierunku, a następnie ręcznie wyjąć i odesłać. Jeśli chodzi o bardzo małą liczbę detali, których zmierzona wartość przecieku osiągnęła lub nawet przekroczyła limit złomu w stole, wypłyną one przez bieżnię przenośnika. Wspomniany powyżej proces wykrywania, przesiewania i przekierowywania realizowany jest przez robota na stanowisku testowym zgrzewania.
Podsumowując, po obróbce impregnacyjnej cylindrów aluminiowych i innych części nie tylko zmniejsza się ilość odpadów i znacznie poprawia się jakość, ale także zmniejsza się koszt produkcji w założeniu zapewnienia jakości, a wydajność jest skutecznie poprawiana. Dlatego w procesie, w którym współczesny przemysł silników samochodowych staje się coraz lżejszy, naukowe i rozsądne wykorzystanie technologii infiltracji jest najlepszym rozwiązaniem, aby całkowicie rozwiązać nieodłączne problemy odlewów ze stopów aluminium i innych lekkich materiałów (takich jak wady, takie jak mikropory).
Proszę zachować źródło i adres tego artykułu do przedruku:Zastosowanie technologii impregnacji w produkcji silników
Minhe Firma odlewnicza są dedykowane do produkcji i zapewniania wysokiej jakości i wysokiej wydajności części odlewniczych (zakres części odlewanych z metalu obejmuje głównie) Cienkościenne odlewanie ciśnieniowe,Odlewanie pod ciśnieniem z komory gorącej,Odlewanie matrycowe w zimnej komorze), Usługa okrągła (usługa odlewania ciśnieniowego,Obróbka CNC,Produkcja form, Obróbka powierzchni). Wszelkie niestandardowe odlewanie ciśnieniowe z aluminium, odlewanie ciśnieniowe magnezu lub znalu / cynku oraz inne wymagania dotyczące odlewów są mile widziane, aby się z nami skontaktować.
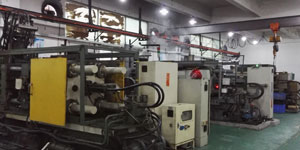
Pod kontrolą ISO9001 i TS 16949, wszystkie procesy są przeprowadzane przez setki zaawansowanych maszyn do odlewania ciśnieniowego, maszyn 5-osiowych i innych urządzeń, od blasterów po pralki Ultra Sonic. Minghe ma nie tylko zaawansowany sprzęt, ale także profesjonalny zespół doświadczonych inżynierów, operatorów i inspektorów, aby zrealizować projekt klienta.
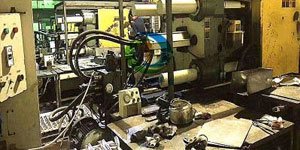
Producent kontraktowy odlewów ciśnieniowych. Możliwości obejmują odlewanie ciśnieniowe aluminium w zimnej komorze od 0.15 funta. do 6 funtów, szybka zmiana konfiguracji i obróbka. Usługi o wartości dodanej obejmują polerowanie, wibrowanie, gratowanie, śrutowanie, malowanie, powlekanie, powlekanie, montaż i oprzyrządowanie. Obrabiane materiały obejmują stopy takie jak 360, 380, 383 i 413.
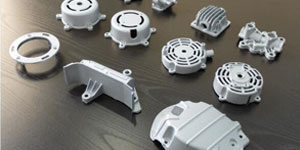
Pomoc w projektowaniu odlewów cynkowych/równoległe usługi inżynieryjne. Zleceniodawca precyzyjnych odlewów cynkowych. Można wytwarzać miniaturowe odlewy, odlewy ciśnieniowe wysokociśnieniowe, odlewy wielopłytkowe, konwencjonalne odlewy formowe, odlewy jednostkowe i niezależne oraz odlewy z uszczelnieniem gniazdowym. Odlewy mogą być produkowane w długościach i szerokościach do 24 cali z tolerancją +/- 0.0005 cala.
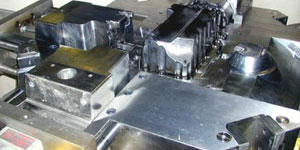
Certyfikowany ISO 9001: 2015 producent odlewanego magnezu, Możliwości obejmują odlewanie ciśnieniowe magnezu do 200 ton gorącej komory i 3000 ton zimnej komory, projektowanie oprzyrządowania, polerowanie, formowanie, obróbka skrawaniem, malowanie proszkowe i płynne, pełna kontrola jakości z możliwościami CMM , montaż, pakowanie i dostawa.
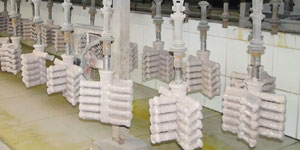
Certyfikat ITAF16949. Dodatkowa usługa odlewania obejmuje casting inwestycyjny,odlewanie piaskowe,Odlewanie grawitacyjne, Utracone odlewanie pianki,Odlewanie odśrodkowe,Odlewanie próżniowe,Trwałe odlewanie form,.Możliwości obejmują EDI, pomoc inżynierską, modelowanie bryłowe i przetwarzanie wtórne.
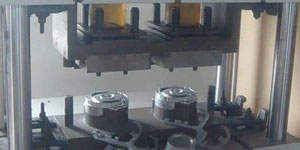
Przemysł odlewniczy Części Studia przypadków dla: samochodów, rowerów, samolotów, instrumentów muzycznych, jednostek pływających, urządzeń optycznych, czujników, modeli, urządzeń elektronicznych, obudów, zegarów, maszyn, silników, mebli, biżuterii, przyrządów, telekomunikacji, oświetlenia, urządzeń medycznych, urządzeń fotograficznych, Roboty, rzeźby, sprzęt dźwiękowy, sprzęt sportowy, narzędzia, zabawki i inne.
W czym możemy Ci pomóc dalej?
∇ Przejdź do strony głównej dla Odlewanie ciśnieniowe Chiny
→Części odlewnicze-Dowiedz się, co zrobiliśmy.
→Powiązane wskazówki dotyczące Usługi odlewania ciśnieniowego
By Producent odlewów ciśnieniowych Minghe |Kategorie: Przydatne artykuły |Materiał tagi: Odlewanie aluminium, Odlew cynkowy, Odlewanie magnezu, Casting tytanu, Odlewanie ze stali nierdzewnej, Odlew mosiężny,Odlew z brązu,Przesyłanie wideo,Historia firmy,Odlew aluminiowy |Komentarze wyłączone