Metoda podawania drutu Proces obróbki żeliwa sferoidalnego
W rzeczywistej produkcji metoda wykrawania i metoda podawania są wykorzystywane do produkcji żeliwa sferoidalnego, a właściwości obu procesów są analizowane. Dzięki porównaniu wszechstronna wydajność odlewów wytworzonych metodą podawania jest bardziej stabilna niż w przypadku metody wykrawania; a proces karmienia ulega sferoidyzacji. Aby podzielić się niektórymi doświadczeniami w nim.
1. Przegląd
Jak wszyscy wiemy, oś jest ważną częścią nośną pojazdu i jest bezpośrednio związana z bezpieczeństwem pojazdu. Obudowa osi jest jednym z kluczowych elementów osi. Właściwości materiału obudowy osi bezpośrednio determinują nośność pojazdu. Obecnie oprawy osi w przemyśle samochodów ciężarowych dzielą się na dwie kategorie: oprawy tłoczone i spawane oraz oprawy odlewane, a oprawy osi odlewane można podzielić na oprawy ze staliwa i oprawy z żeliwa.
Odlewana obudowa osi zawsze zajmowała główną pozycję obudowy osi do ciężkich pojazdów ciężarowych ze względu na dużą nośność i niskie koszty produkcji. Ze względu na trudne warunki pracy obudowy osi i długotrwałą pracę pod obciążeniem dynamicznym wymaga to wysokich wymagań dotyczących właściwości materiałowych obudowy osi. Zapewniając wytrzymałość, musi również uzyskać wyższą plastyczność i twardość, aby dopasować się do obudowy osi. Charakterystyka pracy.
Wiemy, że w przypadku żeliwa sferoidalnego proces sferoidyzacji jest kluczowym ogniwem w produkcji żeliwa sferoidalnego, a jakość obróbki sferoidyzującej bezpośrednio wpływa na jakość żeliwa sferoidalnego. Na początku stosowany przez nas proces sferoidyzacji był procesem sferoidyzacji metodą rush-in. Chociaż ta metoda jest prosta i łatwa w obsłudze, ma wiele wad, takich jak: niska wydajność stopu; duży dym i złe środowisko pracy; reakcja Ilość żużla wytworzonego w tym czasie jest duża; na efekt obróbki łatwo wpływają czynniki zewnętrzne, co prowadzi do wahań jakości odlewów i często bezwarunkowej sferoidyzacji. Te wahania jakości wpłyną na działanie obudowy osi, a nawet wpłyną na bezpieczeństwo pojazdu.
Do produkcji żeliwa zastosowano proces obróbki sferoidyzującej metodą podawania drutu. Zaczęło się w latach 1980. za granicą. Chociaż w krajowej produkcji żeliwa sferoidalnego zaczęto stosować tę technologię późno, technologia ta została szybko spopularyzowana i zastosowana w kraju i jest przydatna do usprawnienia produkcji grafitu sferoidalnego. Efekt stabilności jakości żeliwa jest oczywisty.
2. Proces sferoidyzacji drutu zasilającego
Podstawową zasadą procesu sferoidyzacji podawania nici jest owinięcie określonej kompozycji sproszkowanego środka sferoidyzującego i modyfikatora przez stalową skórę i wysłanie jej do pakietu obróbki sferoidyzującej z określoną prędkością przez urządzenie, tak aby sferoidyzacja na dole pakiet wybuchnie. Aby osiągnąć cel zabiegu inokulacji sferoidyzacyjnej.
Obecnie stosowany przez nas proces sferoidyzacji podawania drutu polega na: dostosowaniu składu chemicznego do wymagań procesu, podgrzaniu do 1510-1520 ℃ i pozostawieniu w bezruchu, temperatura gwintowania wynosi 1480 ~ 1500 ℃, wydajność żelaza wynosi 2 t i temperatura obróbki sferoidyzującej wynosi 1420 ~ 1450 ℃. Temperatura nalewania wynosi 1370~1380℃. Szybkość zaszczepiania z przepływem wynosi 0.1%.
Długość linii sferoidyzacji wynosi 39-46m, dostosowana do zawartości siarki w pierwotnym stopionym żelazie. Im wyższa zawartość siarki, tym dłuższa linia sferoidyzująca musi zostać dodana i odwrotnie. Długość linii zaszczepiania wynosi 32m.
3. Proces sferoidyzacji podawania drutu poprawia jakość odlewów
Po ponad roku produkcji jakość naszych obudów osi uległa znacznej poprawie w porównaniu z poprzednimi. Zwłaszcza stabilność składu, metalografia i właściwości mechaniczne uległy znacznej poprawie.
Porównanie struktury metalograficznej Wybrać to samo położenie odlewu do polerowania i obserwować strukturę metalograficzną. Wykonany obraz metalograficzny pokazano na rysunku 2. W porównaniu z metodą wykrawania kulki grafitowe odlewu wytworzonego metodą podawania są coraz cieńsze, a okrągłość lepsza.
4. Zalety procesu sferoidyzacji nici zasilających
Zgodnie z naszym rzeczywistym porównaniem produkcyjnym, proces sferoidyzacji z podawaniem nici ma wiele zalet w porównaniu z procesem sferoidyzacji metody wykrawania.
- Poprawa środowiska produkcyjnego na miejscu. Gdy środek sferoidyzujący reaguje ze stopionym żelazem, powstaje duża ilość dymu i silne światło, co pogarsza warunki pracy na miejscu; gdy do sferoidyzacji stosowana jest metoda podawania drutu, stanowisko obróbcze Jest pokrywa do przykrycia worka sferoidyzacyjnego, a pokrywa jest połączona z systemem odpylania stacji obróbczej, dzięki czemu dym jest przetwarzany przez system odpylania bycia wypuszczonym bezpośrednio w warsztacie.
- Zmniejsza się ilość dodawanego stopu i zmniejsza się koszt produkcji. Po obliczeniach, przetwarzanie 1t stopionego żelaza metodą podawania stopionego żelaza może zaoszczędzić około 78 juanów kosztów surowca niż metoda impulsowa. Zgodnie z roczną zdolnością produkcyjną 10,000 780,000 ton obudowy osi z żeliwa sferoidalnego naszej fabryki, roczna oszczędność wynosi Koszt to XNUMX XNUMX juanów, a korzyści są znaczne.
- Zrealizuj automatyzację pracy i zmniejsz pracochłonność pracowników. Gdy przeprowadza się proces sferoidyzacji, wstępne przygotowania pracowników są kłopotliwe, w tym ważenie środka sferoidyzującego i modyfikatora, dodawanie środka sferoidyzującego i modyfikatora do worka oraz wymagane są operacje ubijania i pokrywania; dodawana ilość linii sferoidyzujących i zaszczepiających metody podawania nici jest automatycznie dodawana przez szafę sterowniczą, co zmniejsza dużo pracy.
- Jakość sferoidyzacji jest stabilna, a efekt sferoidyzacji lepszy. Według statystyk, od czasu zastosowania procesu sferoidyzacji z podawaniem nici w 2013 r., szybkość przejścia sferoidyzacji wynosi ponad 99.5%, podczas gdy szybkość przejścia procesu sferoidyzacji wynosi tylko 95,%.
5. Jak prawidłowo dobrać parametry procesu sferoidyzacji nici podającej?
W rzeczywistej produkcji prawidłowe dobranie parametrów procesu podawania drutu wymaga weryfikacji pewnej liczby testów. Przeszliśmy wiele dostosowań procesowych od początku organizacji testu do formalnej produkcji masowej. Poniżej podzielimy się naszym doświadczeniem z kolegami.
Aby prawidłowo dobrać parametry procesu sferoidyzacji nici podającej, należy zwrócić uwagę na następujące aspekty:
- (1) Wybór drutu proszkowego Niektóre doświadczenia zagraniczne nie zalecają stosowania drutu proszkowego o wysokiej zawartości Mg. Zbyt duża zawartość Mg, intensywna reakcja sferoidyzacji, duże spalanie Mg i duża ilość żużla. Generalnie zaleca się dobierać zawartość Mg około 30% i stosować nić inokulacyjną zawierającą Ba, która może skutecznie zapobiegać spadkowi inokulacji. Główne parametry stosowanego przez nas drutu proszkowego to: grubość zewnętrznej osłony stalowej to 0.4mm, a średnica drutu rdzeniowego to 13mm. Przed użyciem sprawdź, czy wygląd drutu rdzeniowego powinien być okrągły i wolny od pęknięć, wycieków proszku itp. W rzeczywistej produkcji konieczne jest dostosowanie do temperatury obróbki i wysokości stopionego żelaza. Ogólnie rzecz biorąc, im wyższa temperatura obróbki, tym wyższa wysokość stopionego żelaza i szybsza prędkość podawania drutu. Ponadto. Niektóre materiały wprowadziły również wygodną i wykonalną metodę pomiaru optymalnej prędkości podawania drutu: najpierw zmierz wysokość stopionego żelaza w worku obróbkowym, a następnie ręcznie podawaj drut tak, aby drut rdzeniowy dotykał powierzchni cieczy, a następnie wyczyść licznik, Ręczny podajnik drutu wykonuje podawanie drutu. Gdy usłyszysz dźwięk odpowiedzi „wysięgnika”, natychmiast sprawdź długość podawania. Jeśli ta długość jest zasadniczo równa wysokości stopionego żelaza, prędkość powinna być odpowiednia. Po weryfikacji wybraliśmy prędkość podawania 30m/min.
- Dobór wielkości posuwu nici Właściwą wielkością posuwu nici jest posuw najmniej rdzeniowej nici przy założeniu zapewnienia efektu sferoidyzacji. Ilość podawanego drutu należy określić zgodnie z objętością przetwarzania stopionego żelaza, temperaturą przetwarzania i zawartością siarki w stopionym żelazie. Zgodnie z naszymi pierwotnymi wymaganiami dotyczącymi zawartości siarki stopionego żelaza i procesu produkcyjnego, w połączeniu z weryfikacją eksperymentalną, pod warunkiem zapewnienia resztkowej zawartości magnezu, długość linii sferoidyzacyjnej wynosi 39-46m, a długość linii zaszczepiania wynosi 32m.
- Wybór temperatury obróbki Temperatura obróbki powinna być maksymalnie obniżona, aby zapewnić odpowiednią temperaturę nalewania. Im niższa temperatura obróbki, tym wyższa szybkość wchłaniania magnezu i mniejsze zużycie drutu rdzeniowego. Zgodnie z rzeczywistymi testami produkcyjnymi, czas od rozpoczęcia obróbki sferoidyzującej do rozpoczęcia nalewania wynosi 4 do 5 minut, podczas których spadek temperatury wynosi 40 do 50°C, a czas reakcji sferoidyzującej wynosi 80 do 90 sekund. Ponieważ proces sferoidyzacji musi zostać odwrócony, ustawiamy temperaturę przetwarzania na 1410~1450℃, górna granica jest przyjmowana, gdy temperatura w pomieszczeniu jest niższa niż 5℃, a dolna granica, gdy temperatura w pomieszczeniu jest wyższa niż 25℃.
- Dobór resztkowej zawartości magnezu w stopionym żelazie po obróbce. Resztkową zawartość magnezu należy odłożyć na pewną ilość magnezu zgodnie z charakterystyką samego odlewu. Początkowo kontrolowaliśmy zawartość resztkowego magnezu do 0.03% do 0.06%, ale po rzeczywistej weryfikacji produkcji bardziej odpowiednie jest kontrolowanie zawartości resztkowego magnezu do 0.05% do 0.06%, ponieważ stwierdziliśmy, że gdy resztkowy magnez jest mniejszy niż 0.04%, grafit Nieco gorsza jest krągłość kulki. Gdy jest wyższy niż 0.07%, cementyt ma skłonność do pojawiania się, a tendencja do skurczu stopionego żelaza staje się większa.
- Rozwiązywanie problemu zacinania się drutu podczas użytkowania Zjawisko zacięcia drutu wystąpi podczas procesu przenoszenia drutu rdzeniowego, co spowoduje złomowanie całego pakietu stopionego żelaza. W tym celu podjęliśmy następujące działania: jeden polega na zainstalowaniu stalowego pierścienia nad szpulą drutu rdzeniowego, jak pokazano na rysunku 5, co może zmniejszyć wyginanie drutu rdzeniowego i sprawić, że będzie on płynnie wchodził do mechanizmu prowadzącego; drugi polega na połączeniu dwóch cewek Podczas spawania, po spawaniu, wypoleruj większe nierówności, aby zapobiec zakleszczeniu drutu podczas procesu przenoszenia; po trzecie, należy unikać zagięć o średnicy mniejszej niż 1 m w rurociągu transportującym lub trasie drutu proszkowego, aby zapobiec jego transportowaniu Wyciek proszku lub zakleszczenie podczas procesu
Wnioski 6
- Proces sferoidyzacji metodą drutu zasilającego ma niską ilość dodatku stopu, wysoki współczynnik absorpcji Mg i może skutecznie zmniejszyć dym i silne zanieczyszczenie światłem w warsztacie, zapewniając dobre korzyści ekonomiczne i środowiskowe dla przedsiębiorstw odlewniczych.
- Proces sferoidyzacji metody podawania nici może skutecznie zmniejszyć wskaźnik awaryjności sferoidyzacji, poprawić jakość żeliwa sferoidalnego, poprawić jego wszechstronne właściwości mechaniczne i zwiększyć konkurencyjność rynkową przedsiębiorstwa.
- Każda odlewnia powinna dobrać odpowiednie parametry procesu sferoidyzacji drutu zgodnie z własnymi warunkami produkcji i wymaganiami procesu produkcyjnego, w połączeniu z doświadczeniem produkcyjnym innych producentów.
Proces sferoidyzacji linii zasilającej może znacznie poprawić stabilność jakości żeliwa sferoidalnego, obniżyć koszty produkcji, poprawić środowisko produkcyjne i zmniejszyć pracochłonność pracowników. To najnowszy trend rozwojowy procesu sferoidyzacji.
Proszę zachować źródło i adres tego artykułu do przedruku: FEeding Wire Method Proces obróbki żeliwa sferoidalnego
Minhe Firma odlewnicza są dedykowane do produkcji i zapewniania wysokiej jakości i wysokiej wydajności części odlewniczych (zakres części odlewanych z metalu obejmuje głównie) Cienkościenne odlewanie ciśnieniowe,Odlewanie pod ciśnieniem z komory gorącej,Odlewanie matrycowe w zimnej komorze), Usługa okrągła (usługa odlewania ciśnieniowego,Obróbka CNC,Produkcja form, Obróbka powierzchni). Wszelkie niestandardowe odlewanie ciśnieniowe z aluminium, odlewanie ciśnieniowe magnezu lub znalu / cynku oraz inne wymagania dotyczące odlewów są mile widziane, aby się z nami skontaktować.
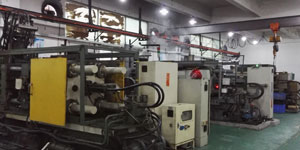
Pod kontrolą ISO9001 i TS 16949, wszystkie procesy są przeprowadzane przez setki zaawansowanych maszyn do odlewania ciśnieniowego, maszyn 5-osiowych i innych urządzeń, od blasterów po pralki Ultra Sonic. Minghe ma nie tylko zaawansowany sprzęt, ale także profesjonalny zespół doświadczonych inżynierów, operatorów i inspektorów, aby zrealizować projekt klienta.
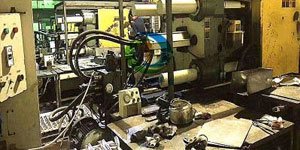
Producent kontraktowy odlewów ciśnieniowych. Możliwości obejmują odlewanie ciśnieniowe aluminium w zimnej komorze od 0.15 funta. do 6 funtów, szybka zmiana konfiguracji i obróbka. Usługi o wartości dodanej obejmują polerowanie, wibrowanie, gratowanie, śrutowanie, malowanie, powlekanie, powlekanie, montaż i oprzyrządowanie. Obrabiane materiały obejmują stopy takie jak 360, 380, 383 i 413.
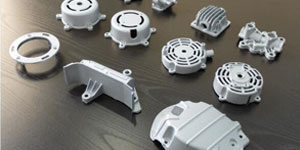
Pomoc w projektowaniu odlewów cynkowych/równoległe usługi inżynieryjne. Zleceniodawca precyzyjnych odlewów cynkowych. Można wytwarzać miniaturowe odlewy, odlewy ciśnieniowe wysokociśnieniowe, odlewy wielopłytkowe, konwencjonalne odlewy formowe, odlewy jednostkowe i niezależne oraz odlewy z uszczelnieniem gniazdowym. Odlewy mogą być produkowane w długościach i szerokościach do 24 cali z tolerancją +/- 0.0005 cala.
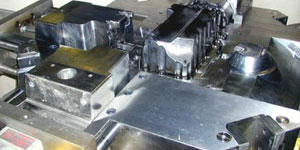
Certyfikowany ISO 9001: 2015 producent odlewanego magnezu, Możliwości obejmują odlewanie ciśnieniowe magnezu do 200 ton gorącej komory i 3000 ton zimnej komory, projektowanie oprzyrządowania, polerowanie, formowanie, obróbka skrawaniem, malowanie proszkowe i płynne, pełna kontrola jakości z możliwościami CMM , montaż, pakowanie i dostawa.
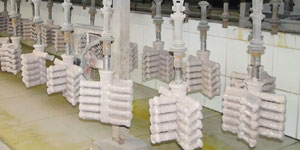
Certyfikat ITAF16949. Dodatkowa usługa odlewania obejmuje casting inwestycyjny,odlewanie piaskowe,Odlewanie grawitacyjne, Utracone odlewanie pianki,Odlewanie odśrodkowe,Odlewanie próżniowe,Trwałe odlewanie form,.Możliwości obejmują EDI, pomoc inżynierską, modelowanie bryłowe i przetwarzanie wtórne.
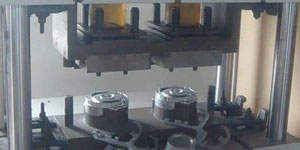
Przemysł odlewniczy Części Studia przypadków dla: samochodów, rowerów, samolotów, instrumentów muzycznych, jednostek pływających, urządzeń optycznych, czujników, modeli, urządzeń elektronicznych, obudów, zegarów, maszyn, silników, mebli, biżuterii, przyrządów, telekomunikacji, oświetlenia, urządzeń medycznych, urządzeń fotograficznych, Roboty, rzeźby, sprzęt dźwiękowy, sprzęt sportowy, narzędzia, zabawki i inne.
W czym możemy Ci pomóc dalej?
∇ Przejdź do strony głównej dla Odlewanie ciśnieniowe Chiny
→Części odlewnicze-Dowiedz się, co zrobiliśmy.
→Powiązane wskazówki dotyczące Usługi odlewania ciśnieniowego
By Producent odlewów ciśnieniowych Minghe |Kategorie: Przydatne artykuły |Materiał tagi: Odlewanie aluminium, Odlew cynkowy, Odlewanie magnezu, Casting tytanu, Odlewanie ze stali nierdzewnej, Odlew mosiężny,Odlew z brązu,Przesyłanie wideo,Historia firmy,Odlew aluminiowy |Komentarze wyłączone